MAGAZYN
13 ryzyk związanych z eksploatacją i obsługą regałów
Tak, dokładnie 13. Celowo nawiązujemy do tej feralnej liczby, gdyż każde z omawianych poniżej zagrożeń może pośrednio, a częściej bezpośrednio spowodować tragedię. Trudno będzie jednak w obecności ubezpieczyciela (lub gorzej – prokuratora) szukać korelacji pomiędzy pechem a zaniedbaniem.
Data publikacji: 20.11.2023
Data aktualizacji: 20.11.2023
Podziel się:
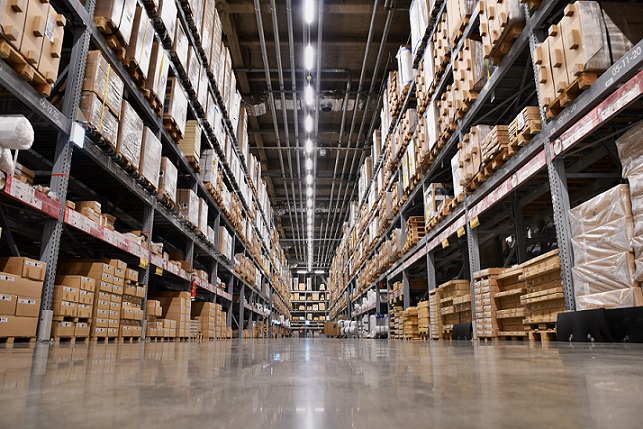
Każda z wymienionych w tekście kategorii stanowi podstawę wystąpienia zagrożenia, a temu należy zapobiegać. Mówimy wówczas o ryzykach i konieczności ich eliminowania lub minimalizowania. Tylko dlaczego o tym mówimy?
Zgodnie z zapisami zawartymi w obligatoryjnych aktach normatywnych każdy pracodawca (zarządca magazynu) jest zobowiązany do przeprowadzania ocen ryzyka w magazynie, poprzez które dąży do zapewnienia możliwie wysokiego stopnia bezpieczeństwa ludzi oraz majątku. To wszystko trzeba robić, aby wiedzieć, jakie działania należy podjąć, aby te ryzyka zminimalizować do akceptowalnego stopnia.
Taka ocena ryzyka odbywa się poprzez analizę różnych potencjalnych zdarzeń niepożądanych, jakie mogą się wydarzyć w magazynie. Są ich oczywiście setki i analizuje się je podczas właśnie ocen ryzyka, ewentualnie podczas profesjonalnego audytu BHP, który wykracza poza banalne check-listy, gdzie ocena zero-jedynkowa jest znacznym uproszczeniem tematu.
A ponieważ regały są jednym z trzech największych źródeł zagrożeń w magazynie, to wypadałoby sprawdzić, jakie są najczęstsze przyczyny pojawiania się zagrożeń w ich obszarze.
Nieprawidłowa obsługa regałów
Obciążenia udarowe
Uderzenia w słupy, zbyt dynamiczne odstawianie ładunków na belkach czy uderzenia w belki nie stanowią najmniejszego problemu dla trzytonowego wózka z jednotonowym ładunkiem. Przy prędkości jazdy 10 km/h prawdopodobnie od razu załatwimy regały w całym magazynie, a przy dobrym monitoringu społeczność internetowa otrzyma kolejny świetny materiał pokazujący, jak łatwo jest pogrzebać się w stosie tysięcy ładunków.
Regały nie są projektowane na przyjmowanie takich uderzeń, a operatorzy powinni być o tym dobrze poinformowani, choćby dla własnego bezpieczeństwa. Uderzenie wózkiem w słup w przypadku w pełni obciążonego regału, z dużym prawdopodobieństwem, skończy się jego zawaleniem.
Przeciążenie miejsca, gniazda lub całej sekcji regałowej czy też nierównomierny rozkład ciężaru w miejscu składowania powoduje uginanie belki, wyboczenie słupa, a czasami prowadzi do natychmiastowego jego złamania. Z reguły jest to ewidentna wina operatora lub systemu, który pozwolił na wprowadzenie do regałów ładunku niezgodnego z projektem. W skrajnym wypadku przeciążenie elementu regału prowadzi do jego zawalenia.
Chodzi tu głównie o „przeciąganie” ładunkiem po belkach albo napieranie na tzw. back-stopy. To pierwsze to kwestia kultury pracy operatorów i nie wypada, aby dobry wózkowy pozwalał sobie na takie rzeczy, bo jeśli ktoś dobrze się postara, to wywróci cały regał. To drugie to już kompletne nieporozumienie.
Należy wiedzieć, że ogranicznik położenia palety nie służy do tego, aby ograniczać położenie palety! Ogranicznik zapobiega niepożądanym skutkom zbyt dalekiego wsunięcia palety w regale, ale operator nie powinien traktować ogranicznika jako elementu „oporowego”, przy którego „dotknięciu”, palety nie wstawia się już dalej. Warto doczytać wyjaśnienie tego zagadnienia zawarte w jednym z biuletynów PSTM.
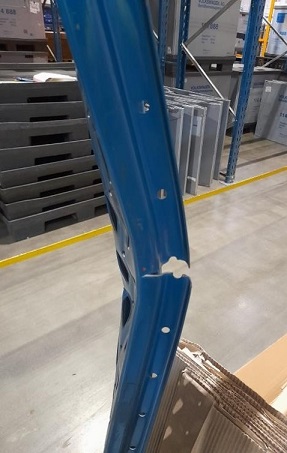
Rys. 1. Poważne zniszczenie słupa
Nieprawidłowa eksploatacja regałów
Zmiany w konfiguracji regałów
Niestety, ale firmami, które najczęściej pozwalają sobie na ten zabieg, są te przedsiębiorstwa, u których widzę też najwyższą dbałość o bezpieczeństwo. Operatorzy logistyczni, magazyny e-commerce itp. obracają różnymi ładunkami, a zmiana klienta lub asortymentu wiąże się często z koniecznością rekonfiguracji regału. A tego nie można wykonywać bez zgody dostawcy.
Co więcej, ingerencje te w konsekwencji zmieniają parametry użytkowe regałów – często na gorsze – i wtedy pojawia się problem. Dodatkowo zmianie uległa jakiś czas temu norma EN-15512 i zrobiło się jeszcze ciekawiej w przypadku regałów kupionych za czasów starej wersji normy, a poddanych modyfikacjom za czasów nowej wersji. Zmiana konfiguracji poprzez podniesienie poziomu belkowego, najprościej rzecz ujmując, powoduje wydłużenie „gołej” części słupa i zwiększenie jego podatności na wyboczenie. A przy obecności jeszcze malutkiego uderzenia, nokaut słupa (z całym późniejszym efektem domina) jest stosunkowo prosty.
Niewłaściwa eksploatacja
Właściwa eksploatacja to nie tylko obsługa regału (wprowadzanie i wyprowadzanie ładunku), ale cały szereg dodatkowych czynności. Wśród błędów związanych z eksploatacją można wyróżnić: niewykonywanie napraw, nieprzeprowadzanie przeglądów regałów, niestosowanie wystarczającej liczby elementów ochronnych, wprowadzanie do regałów niewłaściwych ładunków, nieuzupełnianie brakujących zawleczek (a powinno się!) i wiele innych.
Za takie błędy traci się gwarancję, stwarza się pierwsze niebezpieczne uwarunkowania, traci możliwość rozpoznania błędów w odpowiednio krótkim czasie czy też uszkadza się sam regał.
Elementy niemechaniczne
Z eksploatacją wiąże się również aspekty „niemechaniczne”, takie jak prowadzenie ewidencji stanu regałów, ich napraw, aktualizacji projektów, gromadzenie raportów z przeglądów czy też posiadanie tabliczki i samej dokumentacji, która oczywiście powinna być poprawna.
Braki w tych elementach to błędy proceduralne, a ich występowanie jest wskazywane podczas przeglądu regałów, przy czym brak dokumentacji jest złamaniem wytycznych obligatoryjnych i wskazuje na niedbałość posiadacza regałów.
Przyczyny niewidoczne i postępujące
Niewidoczne uszkodzenia
Trudna sprawa, bo jak wyeliminować uszkodzenie, którego się nie widzi? Tak czasem bywa i norma EN-15635 też o tym wspomina. Ponieważ nie jest możliwe dokładne przeprowadzenie oględzin regału przy jego wypełnieniu ładunkami, czynności te należy wykonywać w sposób kroczący, przy jednoczesnym zachowaniu tzw. hierarchicznego przeglądu regałów. To oznacza, że trzeba realizować zarówno przeglądy eksperckie, jak również krótkookresowe. Za to odpowiedzialny jest PRSES.
Uszkodzenia niewidoczne również nie biorą się znikąd. Aby ich uniknąć, należy uwrażliwić zespół na potencjalne skutki uszkodzeń, zachęcić do zgłaszania rozpoznanych błędów i monitorować bezustannie swoje regały.
Korozja
Najczęściej dochodzi do niej w chłodniach, mroźniach oraz na zewnątrz. To ostatnie zostawiamy na inną okazję, bo ile można pisać, że 99% instalacji w hurtowniach budowlanych (regały zewnętrzne, zadaszone lub nie, z reguły rzędowe lub wspornikowe, zamontowane na kostce brukowej lub wmurowane w podłoże) nie spełnia oczekiwań norm projektowych choćby dlatego, że kłania się nam tu „budowlanka”, która jest kompletnie pominięta w jakimkolwiek planowaniu.
Korozja potrafi zadziać się w wewnętrznej części belki lub słupa, a bardzo często też w stopie. Czesto dochodzi do tego w magazynach, gdzie ściany to najtańsza blacha „trapezówa”, a w magazynie mocno czuć wpływ zewnętrznych warunków atmosferycznych. Skorodowany element potrafi się w nieoczekiwany sposób złamać, co w przypadku słupa może się skończyć niezbyt szczęśliwie.
Zaniedbania w konserwacji
Konserwacja, czyli dbałość o prawidłowy stan techniczny, wymaga określonych działań. Trzeba uzupełniać brakujące elementy, przyglądać się i korygować odchylenia od pionu, wymieniać elementy uszkodzone na nieuszkodzone, a wszelkie sytuacje wątpliwe traktować rygorystycznie (jak np. skręcone słupy czy sfalowane elementy).
Zaniedbania w procedurze konserwacji to najczęściej smutna mina inspektora regałowego i jeszcze smutniejsza mina pani od zakupów, która po zapoznaniu się z raportem, musi wydać niemałą sumę pieniędzy na doprowadzenie regałów do 100% poprawności.
Przyczyny związane z konstrukcją
Błędny montaż lub posadzka
Błędne montaże to nic nadzwyczajnego, a już szczególnie w sytuacji, kiedy nie do końca została przemyślana sprawa związana ze współzależnościami pomiędzy regałami i posadzką.
Błędny montaż to ryzyko nieprawidłowego przenoszenia obciążeń, np. w wyniku zbyt mocno pochylonych słupów, zbyt wąskiej drogi dla wózków, niewłaściwych układów stężeń i paru innych. Z kolei przygody z posadzką to np. zbyt duży nacisk punktowy i pękanie posadzki przy słupach, instalacja zbyt blisko dylatacji i wątpliwości przy mocowaniu albo „klawiszowanie” posadzki, które pojawiają się chwilę po uruchomieniu magazynu.
Korygowanie montażu czy posadzek to niemałe wydatki i mnóstwo problemów.
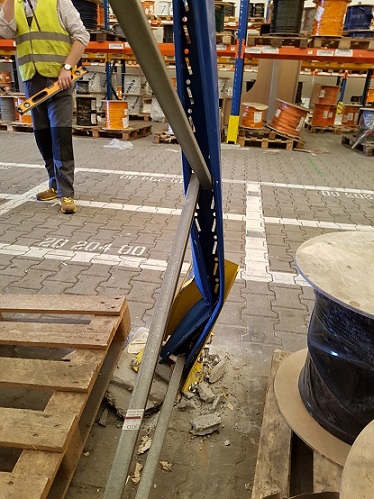
Rys. 2. Zniszczenie ramy regałowej zamontowanej nie niedostosowanym do regałów podłożu
Błędny projekt lub konfiguracja
Błędne projekty zdarzają się wszystkim – belki zostały dobrane do zbyt lekkich ładunków, rama jest zbyt słaba, czasami projekt specjalistyczny nie uwzględnia czegoś istotnego, albo regały nie uwzględniają zagrożeń sejsmicznych. Oczywiście nie dotyczy to nas, ale koledzy z Włoch czy Grecji, których obowiązują te same normy, mają ostatnio nieciekawie, bo dokument EN16681 nakłada nieco więcej wymogów niż w przypadku magazynu położonego w strefie o niskim zagrożeniu trzęsieniem ziemi.
Według badań około 60% regałów zamocowanych we Włoszech nie spełnia wymagań powyższej normy, a trzęsienia ostatnio się nasiliły. Jakie mogą być konsekwencje „niedoprojektowanych” regałów łatwo sobie wyobrazić.
Dokonywanie zmian w konstrukcji
Mamy tu jeszcze niemały zbiór skrajnie (nie)ciekawych zachowań. O ile tryskacze czy hydranty zamocowane do regałów w uzgodnieniu z projektantem nie stanowią problemu, to jednak mocowanie regałów do ścian i sufitów, stosowanie nieoryginalnych części, autorskie przeróbki ślusarskie, wzmacnianie regałów drewnianymi klockami czy też kotwienie słupów „centralnie w dylatacji” stanowią niezbity dowód na nieznajomość specyfiki regałów magazynowych. W obecności tego typu atrakcji wydarzyć może się wszystko.
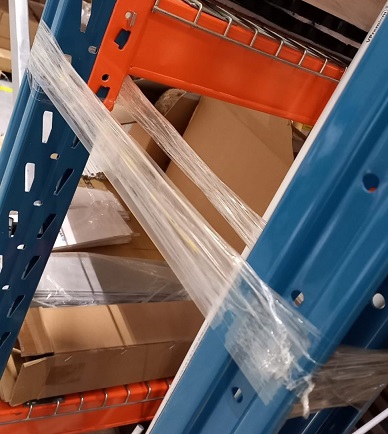
Rys. 3. Karykaturalna postać łącznika ram
Przyczyna specjalna
Brak osoby PRSES
Zobowiązaniem, które przyjmuje kupujący regały, jest wyznaczenie osoby PRSES, chyba że są to jakieś specjalne regały, które nie mają związku z normą EN-15635. Zarządca magazynu ma obowiązek wyznaczyć takiego specjalistę i w myśl rozwinięcia ww. akronimu nadaje mu odpowiedzialność związaną z bezpieczeństwem użytkowania regałów. A tu zadań jest niemało, bo tyle, że można byłoby mówić o tym przez dwudniowe szkolenie. Brak takiej osoby to w zasadzie brak pośredniej lub bezpośredniej kontroli nad wszystkimi poprzednimi rodzajami zdarzeń, sytuacji oraz zaniedbań.
W powyższym materiale dotknęliśmy tylko te elementy, które są związane z obsługą i eksploatacją. Nie omówiliśmy szczegółów przepisów, organizacji, elementów niezwiązanych z mechaniką regałów, aspektu spoin, sposobów usuwania uszkodzeń, regałów używanych (!), kotew oraz wielu innych elementów mających wpływ na bezpieczne użytkowanie regałów. Wszystko to stwarza realne ryzyko wystąpienia zagrożeń, które przy zaistnieniu określonych uwarunkowań prowadzi do wypadków z udziałem ludzi, zniszczeń regałów, strat w majątku i tych najgorszych katastrof konsumujących wszystkie powyższe na raz. A skoro już wiemy, że ryzyku trzeba zapobiegać, zapraszam na wycieczkę do własnego magazynu z poniższym artykułem w ręku.
Tomasz Chojnacki
Inżynier logistyk, projektant, inspektor regałowy, audytor, doktorant na WT PW. Zrealizował ponad 70 projektów magazynów w Polsce i za granicą, a także 200 audytów, przeglądów regałów oraz ekspertyz specjalistycznych w magazynach. Wiceprezes PSTM i Przewodniczący Komitetu ds. Szkoleń tamże.
https://wdx.pl/
Mateusz Sadowski
Inspektor Regałowy w firmie WDX S.A., biegły w normach technicznych związanych z eksploatacją regałów. Realizuje przeglądy regałów, inwentaryzacje systemów składowania oraz profesjonalne dokumentacje i rysunki techniczne.
https://wdx.pl/
Tomasz Ledwoch
Inspektor Regałowy w firmie WDX S.A., doświadczony w przeglądach technicznych maszyn i urządzeń. Realizuje przeglądy regałów, szkolenia, inwentaryzacje. Uprawniony do prac na wysokości. Członek PSTM.
https://wdx.pl/
Zobacz również