MAGAZYN
Ograniczanie kosztów opakowań w łańcuchu dostaw
W naszej aktualnej kryzysowej rzeczywistości jesteśmy bardzo zorientowani na wszelkiego rodzaju redukcje kosztów, ale każdą z nich należy wdrażać z głową, aby nasze cele nie były osiągane tylko i wyłącznie pozornie. To proste stwierdzenie znajduje swoje odzwierciedlenie również w kontekście ograniczania kosztów opakowań w łańcuchu dostaw i trendów, które dość wyraźnie kształtują się w tym zakresie.
Data publikacji: 27.03.2023
Data aktualizacji: 14.08.2023
Podziel się:
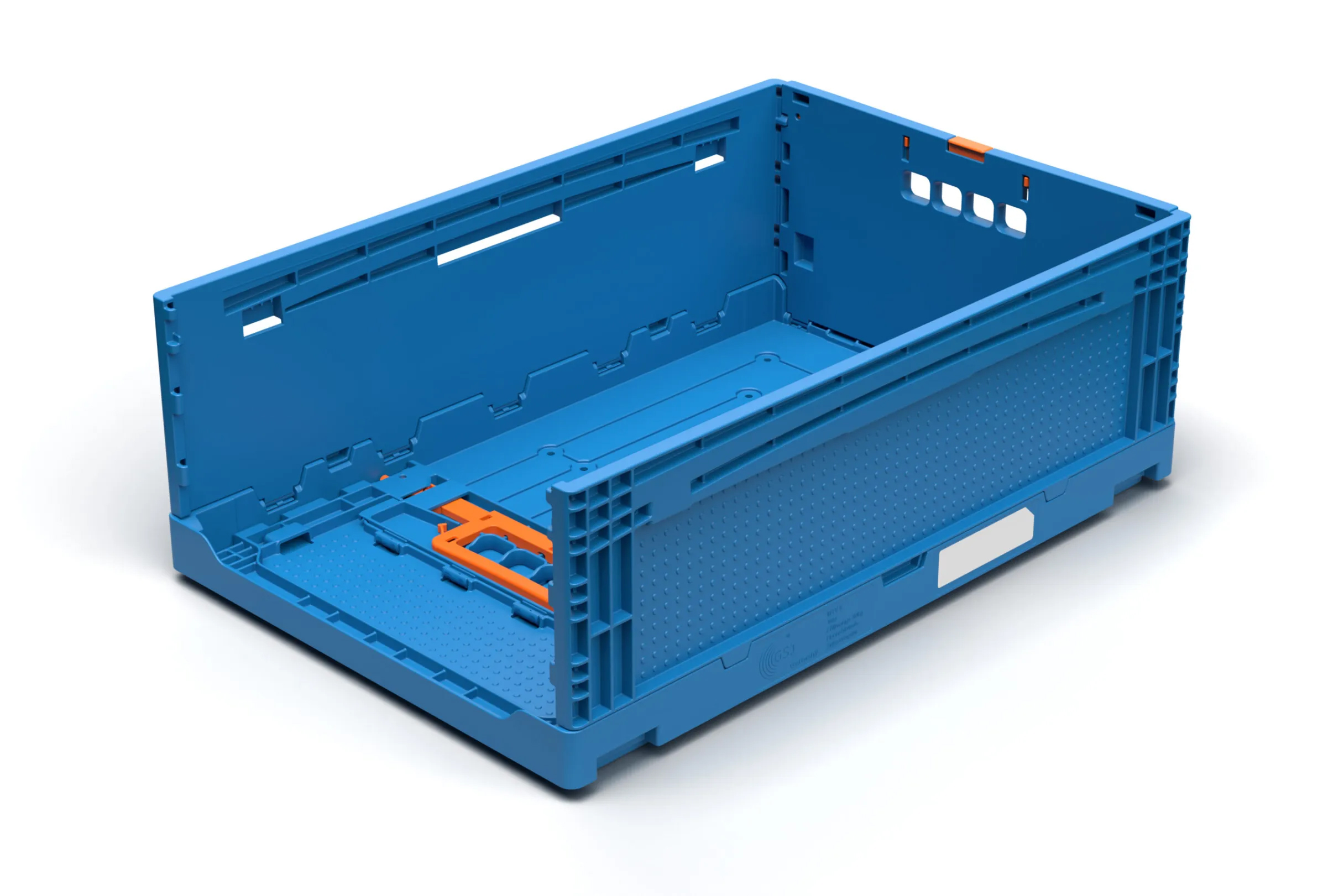
POZORNE KORZYŚCI
Wracając do pozornych optymalizacji – nie chcielibyśmy, aby np. nasz dział zakupów, motywowany presją redukcji ceny komponentów, zgodził się na zwiększenie MOQ (Minimum Order Quantity – minimalnej wartości zamówienia) dla dostawcy, co spowodowałoby zatory w naszym magazynie, który nie jest przygotowany na przyjęcie większej liczby części w dłuższych odstępach czasu. To doprowadziłoby do konieczności wynajęcia dodatkowej zewnętrznej przestrzeni magazynowej, która nie tylko generuje dodatkowe koszty wynajmu, transportu komponentów, zwiększonego czasu reakcji (już nie przejdziemy się do magazynu po komponent, tylko musimy go zamówić i dostaniemy go za kilka godzin lub dopiero następnego dnia), ale i ma wymierny wpływ na płynność finansową organizacji. Dlaczego? Mamy zdecydowanie wyższe zapasy, za które dostawcy należy zapłacić. I choć wydawałoby się, że zasadniczy cel działu zakupów został osiągnięty – przecież obniżono cenę jednostkową – ale kiedy policzymy wszystkie dodatkowe koszty, które opisana „optymalizacja” wywołała, to okaże się, że taniej było płacić wyższą cenę za pojedynczy komponent.
Dlatego tak istotne jest, żeby wszelkie pomysły racjonalizatorskie konsultować ze wszystkimi zainteresowanymi stronami po to, aby uniknąć sytuacji, w których każdy dział kieruje się własnymi celami, nie patrząc na to, jak jego działania wpływają na pozostałe obszary organizacji. Jeśli tak jest, to możemy być niemal pewni, że oszczędności w jednym dziale wywołają lawinę dodatkowych kosztów w innych częściach naszej organizacji. A tego oczywiście chcielibyśmy uniknąć.
CECHY OPAKOWAŃ A MOŻLIWOŚCI OPTYMALIZACJI|
Zatrzymajmy się, przy cechach samych opakowań. Niektóre z nich będą miały wpływ na to, co możemy w omawianym kontekście zoptymalizować. Wybierając najlepsze rozwiązanie dla naszego wyrobu, warto będzie wziąć pod uwagę kilka aspektów:
- Materiał opakowania – tutaj powinniśmy przeanalizować różne alternatywy, bo być może okaże się, że aktualnie stosowane rozwiązanie niekoniecznie nadal jest najbardziej optymalne kosztowo. Zwłaszcza w kontekście jego późniejszej utylizacji.
- Wielkość opakowania, czyli czy nasz wyrób jest optymalnie zapakowany – redukując do niezbędnego minimum przestrzenie między detalami, unikamy efektu „wożenia powietrza”. Do niedawna ważniejszym kryterium wyboru była standaryzacja opakowań, żeby zminimalizować liczbę używanych rozmiarów i rodzajów opakowań. To oczywiste, że przy negocjowaniu jednostkowych cen zakupu ważna jest roczna liczba zamawianych pudełek. To wiązało się z tym, że część wyrobów była pakowana nie do końca efektywnie, generując zdecydowanie wyższe koszty składowania czy transportu. Na szczęście trend ten się zmienia i coraz więcej firm prowadzi analizy porównawcze, które potrafią na liczbach wykazać oszczędności lub ich brak w przypadku wprowadzenia bardziej skomplikowanych rozwiązań.
- Możliwość wdrożenia opakowania zwrotnego w działalności B2B – przy rosnących cenach tektury to bardzo kusząca możliwość. W tym kontekście możemy skorzystać nie tylko z zakupu czy leasingu własnych opakowań, ale też nawiązać współpracę z dostawcami, którzy profesjonalnie zajmują się wynajmem (tzw. poolingiem) opakowań czy palet. Ogólnie rzecz biorąc, programy recyklingu czy powtórnego wykorzystania opakowań pomagają zmniejszyć zapotrzebowanie na kupno nowych produktów i docelowo ograniczyć koszty. Oczywiście tego typu rozwiązania są prostsze do wdrożenia w przypadku relacji B2B, ponieważ opakowanie nie spełnia w tym kontekście funkcji dekoracyjnej czy reklamowej, tak jak w przypadku dostaw B2C.
W kontekście wyboru rozwiązań opakowaniowych niezwykle istotne jest też określenie, w którym miejscu łańcucha dostaw się znajdujemy. Powinniśmy tutaj dokładnie przemyśleć naszą pozycję oraz wpływ pozostałych ogniw łańcucha na nasze procesy, dzięki czemu będziemy w stanie nawiązać bliższą współpracę z dostawcami i klientami w zakresie ujednolicenia stosowanych przez nas opakowań lub wspólnego wdrożenia innych rozwiązań mogących przynieść wymierne oszczędności.
KOSZT TO NIE TYLKO ZAKUP
Rozmawiając o kosztach opakowań w łańcuchu dostaw, musimy jasno zdawać sobie sprawę, że nie składa się nie jedynie cena zakupu. Myślę, że można pokusić się tutaj o nieco kontrowersyjne stwierdzenie, że cena zakupu jest tym najmniej istotnym elementem.
Na czym zatem powinniśmy się skupić, analizując koszty opakowań w ujęciu całościowym?
- Elastyczność dostawcy opakowań – czyli jaką liczbę i w jakim czasie jest nam w stanie zrealizować ponad zakontraktowane wolumeny, jeśli zajdzie taka potrzeba.
- Jakość opakowania – w przypadku kartonów będzie to oznaczało bezpieczeństwo naszych wyrobów w transporcie, czyli czy karton nie zapadnie się pod ciężarem, chroniąc towar przed uszkodzeniami, a nas przed reklamacjami. Niemniej należy również sprawdzić, czy kartony, których aktualnie używamy, nie są zbyt masywne, i czy niepotrzebnie nie przepłacamy za wykorzystane miejsce, chociaż nasze potrzeby są mniejsze. Tutaj często istnieje pole do ewentualnej redukcji, co oczywiście wymaga przeprowadzenia prób pakowania. W przypadku opakowań zwrotnych jakość będzie odnosiła się do żywotności pojemnika. Jest to szczególnie istotne przy opakowaniach potrzebnych do kilkuletnich projektów (w branży motoryzacyjnej mówimy zwykle o 8 latach). Możemy kupić tani pojemnik, który wytrzyma 3–4 lata i po tym czasie trzeba będzie wymienić nawet 80% opakowań, albo zainwestować w droższy, który obsłuży nam w całości dany projekt i prawdopodobnie jeszcze kolejny. Zwłaszcza, że w dzisiejszych czasach nie musimy kupować pojemników za gotówkę, bo rynek oferuje różne rodzaje finansowania. Możemy pojemniki wyleasingować lub nawiązać współpracę z firmą, która nie tylko kupi je dla nas, ale może nimi również zarządzać przez czas trwania umowy – składować, myć, naprawiać, dystrybuować. Rozwiązań jest mnóstwo – wystarczy rozejrzeć się na rynku.
- Rozmiar opakowania – tutaj pod rozwagę warto wziąć nie tylko optymalne wykorzystanie środka transportu z uwzględnieniem tego, jakimi autami będziemy wozić nasz towar (wysokość ładowania), ale również sposób składowania czy ilość miejsca na linii produkcyjnej. Jeśli źle określimy wielkość pojemnika, a nie będziemy mieć możliwości przemodelowania ustawienia linii, to może się to wiązać z koniecznością przepakowywania komponentów przed ich dostarczeniem na produkcję lub całkowitą zmianą koncepcji pakowania. A to może być bolesne, jeśli już zamówiliśmy opakowania,
- Sposób składowania pełnych i pustych opakowań – ten punkt będzie istotny zarówno dla kartonów, jak i opakowań zwrotnych. Decydując się na rodzaj opakowania, warto przeanalizować, jak kartony będą do nas dostarczane (na płasko czy rozłożone, czyli gotowe do użycia), gdzie będziemy je składować, czy będziemy mieli do nich swobodny dostęp, jak będziemy je identyfikować. Pamiętajmy, że złożone kartony wyglądają tak samo, zatem przy kilku rodzajach czy wymiarach potrzebna jest metoda ich identyfikacji. I raczej nie sprawdzą się w tym kontekście karteczki wkładane między warstwy kartonów, bo te lubią wypadać, a wtedy zostajemy z paletą niedookreślonych opakowań, co potrafi dać się we znaki, zwłaszcza jeśli okaże się, że zabrakło tych najbardziej krytycznych. Jeżeli zdecydujemy się na usługę przywożenia nam przez dostawcę kartonów rozłożonych, to warto określić możliwą częstotliwość dostaw oraz minimalny czas reakcji, żeby w sytuacji nagłej zmiany planów produkcyjnych nie borykać się z brakiem odpowiedniego opakowania. Przy opakowaniach zwrotnych warto przeanalizować nasze średnie zapotrzebowania na komponenty czy wyroby gotowe i oszacować ilość miejsca potrzebnego na składowanie towarów i pustych pojemników oczekujących na wysyłkę do dostawcy, a także miejsca potrzebnego na przechowywanie pustych pojemników pod naszą produkcję i późniejszego ich składowania już z wyrobem gotowym.
- Czas potrzebny na składanie i rozkładanie pojemników – decydując się na pojemnik zwrotny, warto zwrócić uwagę na takie szczegóły, jak czas potrzebny na złożenie i rozłożenie pojemnika czy poziom hałasu, jaki się przy tym generuje. Dla pojemników o podobnej konstrukcji czas złożenia potrafi różnić się nawet o 30 sekund, co w skali miesiąca czy roku daje nam wymierne oszczędności w pracy operatora. Natomiast poziom hałasu emitowanego przez spadające ścianki pojemnika potrafi być bardzo uciążliwy, dlatego warto to sprawdzić przed ostateczną decyzją o wyborze opakowania.
- Mycie lub naprawa opakowań – ta część analizy dotyczy oczywiście zwykle opakowań zwrotnych, aczkolwiek w przypadku opakowań kartonowych – jeśli zdecydujemy się na ich ponowne wykorzystanie – dojdzie koszt odpowiedniej ich selekcji, co też warto skalkulować. W przypadku mycia czy naprawy musimy wiedzieć, czy będziemy to robić we własnym zakresie, czy raczej zlecimy te czynności na zewnątrz. Jeśli tak, to jak daleko od nas znajduje się nasz usługodawca, jakie minimalne liczby opakowań możemy mu dostarczać, ile czasu będzie on potrzebował na umycie lub naprawę naszych pojemników? Kluczowe jest dookreślenie, ilu opakowań i na jak długo będziemy musieli się pozbyć z obiegu, i czy nie spowoduje to braków w naszych procesach – a w konsekwencji np. konieczności zastosowania opakowania alternatywnego czy przepaku.
- Ewidencja opakowań – jeśli zdecydujemy się na opakowania zwrotne, musimy pamiętać o koniecznym prowadzeniu ewidencji wejść i wyjść. W przeciwnym razie ryzykujemy, że w ciągu roku część naszych pojemników rozproszy się po świecie i możliwe, że nigdy ich nie odzyskamy. Dlatego decydując się na zakup opakowań zwrotnych, powinniśmy myśleć o ludziach, narzędziach i procedurach, które nas w tym obszarze zabezpieczą,
- Utylizacja opakowań – wybierając konkretne opakowanie, musimy pamiętać o jego wpływie na środowisko. Bez względu na to, czy będziemy utylizować opakowania po komponentach, czy nasz klient będzie utylizował opakowania po naszych wyrobach – warto dobierać takie rozwiązania, które nie tylko będą najbardziej ekonomiczne, ale i najmniej obciążające środowisko. A zatem najlepiej takie, które da się poddać procesowi recyclingu po ich cyklu życia.
Powyżej wymieniłam najważniejsze składowe kosztów opakowań poza ceną zakupu. Jest ich oczywiście znacznie więcej, natomiast nie mamy tutaj miejsca, aby je wszystkie opisać.
PODSUMOWANIE
Kilka wskazówek w ramach podsumowania – pamiętajmy, że regularne monitorowanie i analiza kosztów związanych z opakowaniami pozwoli nam na wczesne wykrycie oraz eliminację nieefektywnych praktyk, co oczywiście finalnie przełoży się na niższe opłaty.
Zalecamy też wnikliwą analizę wpływu podejmowanych przez nas działań optymalizacyjnych na inne działy naszej organizacji, abyśmy w zapale szukania oszczędności nie wylali przysłowiowego dziecka z kąpielą, i nie spowodowali znacznie wyższych kosztów dodatkowych, które przeważą zyski z naszych „oszczędności”.
Wierzę, że rok 2023 upłynie czytelnikom magazynu „Logistics Manager” pod znakiem mądrych i przemyślanych decyzji prowadzących do realnych redukcji kosztów.
Autor: Małgorzata Michalik
Więcej o zrównoważonym podejściu do zarządzania pojemnikami i opakowaniami przeczytasz TUTAJ
Zobacz również