ZARZĄDZANIE
Automatyzacja wg rzymskiej maksymy
Jak ocenić opłacalność zastosowania automatyki w logistyce? Zagrajmy w skojarzenia. Zamykamy oczy i wyobrażamy sobie scenę pod tytułem „automatyzacja”. Zauważmy, że nasze pierwsze skojarzenia dotyczą automatyzacji produkcji. Logiczne – produkcja to proces przyrostu wartości. Jeżeli automatyzacja może przyczynić się do zwiększenia efektywności lub do eliminacji błędów, to wspomniany przyrost wartości może sfinansować inwestycję, a stopa zwrotu jest policzalna i namacalna. A jak sytuacja wygląda w logistyce?
Data publikacji: 05.08.2021
Data aktualizacji: 21.06.2023
Podziel się:
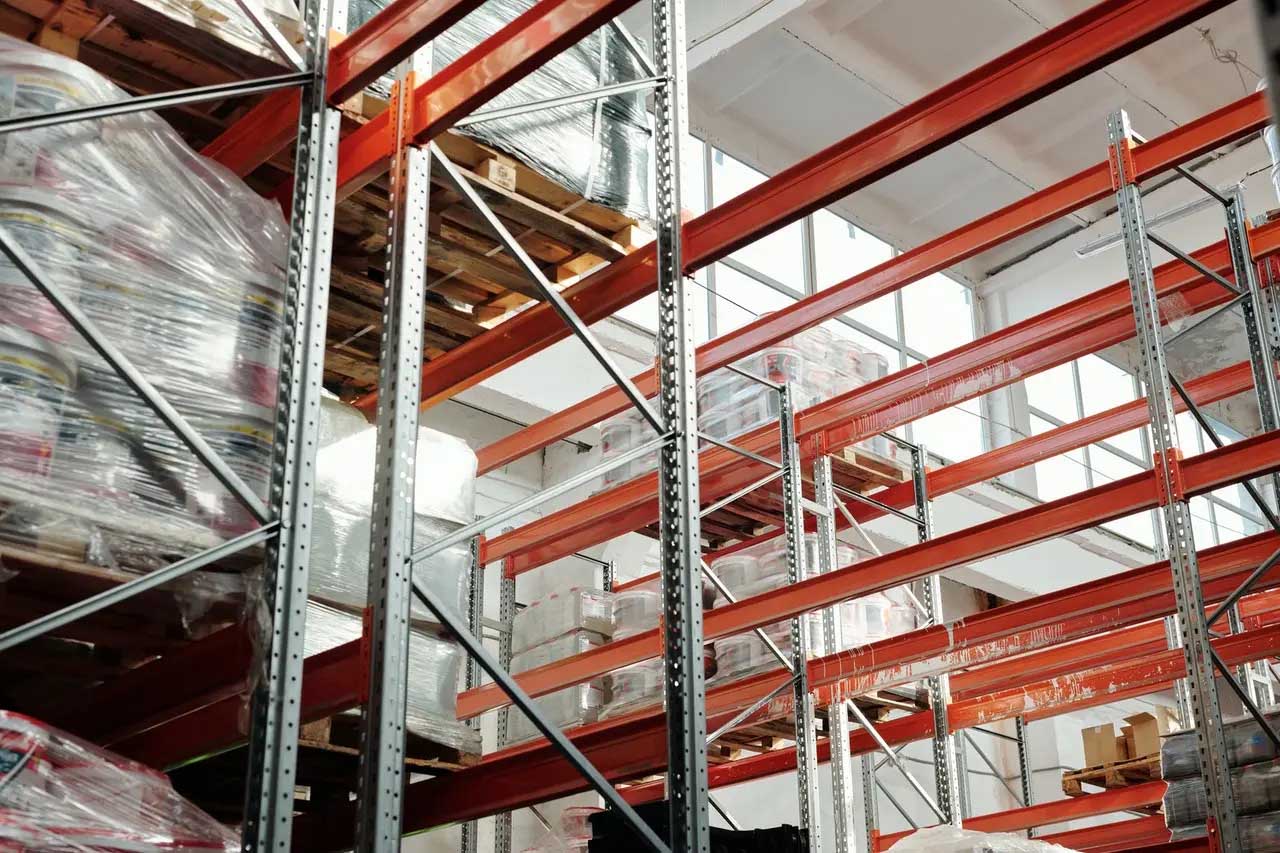
Procesy logistyczne są również niezbędne dla realizacji celów biznesowych firmy, jednak nie są one stricte procesami zwiększającymi wartość produktu, a raczej generującymi koszty. Zatem tutaj nie wytwarzamy wartości dodanej, która sfinansuje nam inwestycję. Oczywiście nie oznacza to, że jakiekolwiek inwestycje w automatykę nie mają tu sensu. Zasadne jest jednak pytanie, jak ocenić opłacalność zastosowania automatyki w logistyce.
Udział procesów logistycznych w tworzeniu wartości dodanej
Po pierwsze zastanówmy się, jak jest z tą wartością dodaną w procesie logistycznym. Czy na pewno nie następuje tu przyrost wartości? Weźmy pod lupę handel detaliczny. Towar na półce sklepowej jest droższy niż towar na wyjściu z linii produkcyjnej. Oznacza to, że klient płaci dodatkowo za udostępnienie produktu w dogodnym do zakupu miejscu. Skoro tak, to w logistycznym procesie dostarczenia produktu na półkę nastąpił jednak przyrost wartości. Proces ten obejmuje nie tylko transport na drodze producent – magazyn – sklep, ale również wszystkie czynności wewnątrz magazynu: przyjęcie, składowanie, kompletację zamówień, pakowanie, przygotowanie jednostek wysyłkowych i wysyłkę. Czynności te mogą być wykonane manualnie z zastosowaniem prostych środków technicznych, bądź też z wykorzystaniem automatycznych urządzeń zastępujących pracę człowieka. Opłacalność zastosowania określonej technologii możemy określić porównując ją z rozwiązaniem manualnym i obliczając różnicę kosztów oraz stopę zwrotu, czyli po jakim czasie oszczędności kosztów sfinansują nam poniesioną inwestycję. Do takiego porównania potrzebne są co najmniej dwie alternatywne koncepcje obejmujące całość procesu magazynowego end-to-end. Koncepcja taka musi zawierać layout z wymiarowaniem stref funkcyjnych, specyfikację zastosowanego wyposażenia, obliczoną wymaganą liczbę personelu oraz oczywiście nakłady inwestycyjne i generowane koszty. Jak taką koncepcję zbudować, na czym skupić największą uwagę i gdzie spodziewać się największych efektów z zastosowania automatyki?
Posłużmy się kilkoma przykładami, skrajnie różniącymi się od siebie.
- Magazyn wyrobów gotowych producenta napojów: kilkadziesiąt SKU, duży wolumen wysyłanych towarów, głównie na paletach jednorodnych, marginalna liczba palet zawierających miks produktów.
- Centrum dystrybucyjne sieci supermarketów: kilka tysięcy SKU, kilka klas temperaturowych (napoje i towary suche, chłodnia, mroźnia, warzywa i owoce), towar kompletowany w jednostkach zbiorczych dla dużych formatów sklepów i w pojedynczych sztukach dla małych sklepów. Jednostki wysyłkowe: palety z miksem produktów o różnych wymiarach, wadze i klasie zgniatalności, palety i półpalety jednorodne z artykułami o najwyższej rotacji.
- Centrum dystrybucji części zamiennych do samochodów: sto kilkadziesiąt tysięcy SKU o bardzo zróżnicowanych parametrach (od dużych elementów karoserii, szyb i ciężkich akumulatorów do drobnych części mieszczących się w dłoni); zróżnicowana rotacja z bardzo wysokim udziałem artykułów wolno rotujących. Zróżnicowane jednostki wysyłkowe: niestandardowe palety z elementami gabarytowymi, paleto-kosze zwrotne i małe paczki kurierskie.
Już na pierwszy rzut oka widać, że w każdym z powyższych przypadków portfolio produktów, struktura zamówień i specyfika biznesu powoduje, że procesy magazynowe i kreowana w nich wartość dodana skrajnie różnią się od siebie. W konsekwencji oczywiście możliwe do zastosowania techniki i potencjalne korzyści z zastosowania automatyki też są zróżnicowane. Zajrzyjmy zatem do wnętrza tych magazynów.
Magazyn napojów
W tym magazynie, ze względu na małą ilość SKU, duże wolumeny i jednorodność jednostek ładunkowych, króluje najprostsza z technik magazynowych: składowanie blokowe na posadzce – tanie i zapewniające dobrą gęstość składowania. Potencjał zastosowania automatyki w składowaniu jest tu praktycznie zerowy. Powinniśmy natomiast skupić uwagę na procesach transportu z końcówki linii rozlewniczej do magazynu oraz na załadunku. Tu zależy nam na szybkości i efektywności, tu też najczęściej powstają wąskie gardła ze względu na duże wolumeny i znaczne strumienie materiałów. Komponentami naszych koncepcji mogą być wszelkie techniki automatycznego transportu jednostek paletowych, budowania miksu palet na ciężarówkę i automatycznego załadunku pojazdów.
Centrum dystrybucyjne sieci supermarketów
Tutaj punkt ciężkości naszej uwagi znajduje się w procesie kompletacji. Angażuje ona ponad 60 proc. pracochłonności i zasobów ludzkich w tego typu magazynie. Techniki wspomagające proces kompletacji, eliminujące błędy ludzkie oraz minimalizujące (lub eliminujące) wysiłek ludzki w operowaniu ciężkimi jednostkami (np. zgrzewki, skrzynki z napojami), powinny znaleźć się w obszarze naszych zainteresowań. Dodatkowo, synchronizacja pracy różnych stref temperaturowych, zarządzanie buforami załadunkowymi oraz szybkim procesowaniem artykułów ultraświeżych z minimalnym (lub zerowym) zapasem stawiają specjalne wymagania systemowi zarządzania magazynem i jego interfejsom z układami automatyki. Osobnym obszarem mogącym wkrótce wymagać szczególnej uwagi jest mroźnia. Ze względu na trudne warunki pracy w bardzo niskiej temperaturze coraz trudniej jest pozyskać pracowników, co może wkrótce wymusić stosowanie automatycznego składowania i kompletacji w tej strefie – nawet gdy payback inwestycji nie będzie atrakcyjny.
Centrum dystrybucji części zamiennych
To najbardziej złożony z omawianych przykładów. Różnorodność składowanych i procesowanych artykułów w tym magazynie pociąga za sobą mnogość możliwych do zastosowania technik. Duże znaczenie ma efektywność zagospodarowania dostępnej kubatury magazynu: techniki zapewniające wysoką gęstość składowania powinny być dobrane do charakterystyki składowanych produktów i zgrane z pozostałymi procesami w magazynie. Kompletacja jest tutaj również kluczowym procesem. Przy tak dużej różnorodności i mnogości artykułów, osiągnięcie wysokiej wydajności jest wyzwaniem. Nawet gdy pogrupujemy ponad sto tysięcy SKU w kilkadziesiąt klastrów (ze względu na rotację, gabaryty, jednostki ładunkowe, wymagania specjalne, itp.), a klastry w możliwe do zastosowania techniki, możemy mieć do opracowania i porównania nawet kilkanaście możliwych wariantów organizacji i wyposażenia magazynu. Szczególną uwagę poświęcić należy również systemom IT (od poziomu sterowania procesem do poziomu zarządzania magazynem), aby zapewnić odpowiednią koordynację pracy stref funkcyjnych, terminową konsolidację zleceń przed załadunkiem, efektywne procesowanie zleceń pilnych, obsługę błędów i wyjątków itp. Nawet przy zastosowaniu wysokowydajnych technik, gdy zabraknie dobrego dyrygenta w postaci systemu IT, oczekiwana wydajność procesu end-to-end nie zostanie osiągnięta.
Trójetapowe wdrożenie automatyki
Przedstawiona w powyższych przykładach różnorodność procesowo-techniczna może sugerować, że jednoznaczna recepta na wdrożenie automatyki w magazynie wydaje się niemożliwa do opracowania. Możemy jednak pokusić się o przedstawienie pewnych kluczowych zasad, którymi należy się kierować, aby modernizacja i automatyzacja magazynu zakończyła się sukcesem oraz uwypuklić często popełniane błędy.
Zasada 1: Od ogółu do szczegółu
Każdy złożony problem techniczny należy rozwiązywać etapowo. Dotyczy to również projektowania i realizacji obiektów logistycznych. Rozpocząć należy od zdefiniowania wymagań. Następnym etapem jest koncepcja procesowo-techniczna, koniecznie wielowariantowa, aby możliwy był wybór rozwiązania spełniającego zdefiniowane wymagania przy optymalnych kosztach, nakładach i ryzyku. Po wyborze koncepcji do realizacji następuje uszczegółowienie projektu, koordynacja projektów różnych branż (wyposażenie logistyczne – budynek i technologia budynku – HVAC – ppoż. – IT – media i infrastruktura techniczna itp.), i wybór najlepszych dostawców i wykonawców (włącznie z wyborem optymalnego modelu realizacji inwestycji, np. inwestycja własna w budynek vs. wynajem Built-to-Suit, generalne wykonawstwo vs. integrator technologii i IT vs. koordynacja wielu dostawców itp.). Im późniejszy etap tego procesu, tym wyższy poziom szczegółowości i zakres tematów, które należy dokładnie określić i sprecyzować: nie tylko parametry techniczne, jak wydajności i przepustowości, dyspozycyjność itp., ale również metody ich pomiaru i testów, plan wdrożenia i rozruchu, model serwisowania i wsparcia, przeszkolenie personelu i wiele innych. Często popełnianym błędem jest brak właśnie takiego etapowego podejścia, angażowanie w proces projektowy dostawców już na wczesnym etapie i „nurkowanie” w szczegóły techniczne czy finansowe poszczególnych rozwiązań, bez zbudowania całościowej koncepcji jako bazy dla podjęcia decyzji inwestycyjnej. Taki błąd powoduje również naruszenie drugiej zasady opisanej poniżej.
Zasada 2: Holistyczne podejście
Holizm stawia tezę, że zjawiska tworzą układy całościowe, rządzące się prawidłowościami, których nie jesteśmy w stanie rozpoznać analizując składniki zjawiska w oderwaniu od siebie. Znakomitym przykładem takiego układu całościowego jest właśnie centrum dystrybucyjne: system współzależnych procesów, przetwarzający artykuły o różnorodnej charakterystyce, rotacji, wymogach i ograniczeniach. Dodatkowo, układ ten stanowi ogniwo większej całości, połączone z otoczeniem zarówno przepływem materiałów, jak i informacji. Aby poprawnie zaprojektować i wdrożyć taki sprawnie działający układ, należy właśnie zastosować podejście holistyczne. Traktować centrum dystrybucyjne jak zintegrowany system, uwzględnić współzależności poszczególnych komponentów i procesów, ocenić ich ważność dla całości układu. Ma to znaczenie zarówno przy projektowaniu obiektu od podstaw (greenfield), jak i rozbudowie czy modernizacji istniejącego magazynu. Zwłaszcza w tym drugim przypadku spotykamy się z częstym błędem wyrywkowego podejścia i punktowego rozwiązywania problemów bez całościowej koncepcji. Powstaje samochód ze znakomitym silnikiem i trzema kołami o doskonałych parametrach (każde inne). Jakoś nie potrafi on ruszyć z miejsca.
Zasada 3: Liczby
Podstawą projektu są liczby i to zarówno w ogólnej koncepcji, jak i w projekcie detalicznym. Dotyczy to zarówno danych wejściowych, jak i wyników obliczeń, będących podstawą do podjęcia decyzji inwestycyjnej. Zbudowanie bazy danych do projektu rzutuje na jakość opracowania, stąd dane należy pieczołowicie zebrać, przeanalizować, zidentyfikować i wyeliminować błędy, a brakujące dane zastąpić poprawnymi założeniami. Po drugiej stronie mamy obliczenia: na etapie projektu koncepcyjnego niezbędne są narzędzia do obliczania pracochłonności, wydajności, czasów procesów i liczby personelu, narzędzia wspomagające sizing stref funkcyjnych oraz narzędzia do kalkulacji nakładów inwestycyjnych, kosztów itp. Należy pamiętać, że systemy automatyki nie są tak elastyczne, jak procesy manualne, a więc są znacznie bardziej wrażliwe na błędy. Nie tylko na błędy projektowe, ale również na błędne założenia i dane wejściowe. Dlatego przy bardziej złożonych systemach rekomendowane jest przeprowadzenie symulacji: zbudowanie cyfrowego modelu przyszłego magazynu i przetestowanie go na danych transakcyjnych ekstrapolowanych o prognozowane wzrosty. Symulacja taka ma na celu nie tylko identyfikację możliwych wąskich gardeł i korektę projektu. Za jej pomocą testuje się też wrażliwość systemu na zaburzenia zewnętrzne (np. skok popytu, awaria zasilania, spóźnienie dostawy) oraz wewnętrzne (np. spadek wydajności personelu w jednym z podprocesów, awaria napędu). Symulacja jest też często podstawą dla zbudowania logiki procesu obsługiwanego automatyką i dla opracowania algorytmów dla systemu zarządzania przepływem materiałów.
Omne trinum perfectum
Maksyma starożytnych Rzymian jest tu najlepszym podsumowaniem: wszystko, co potrójne jest doskonałe. Stosujmy zatem w praktyce opisane powyżej trzy zasady:
1) od ogółu do szczegółu,
2) holistyka,
3) liczby.
Rozwiązujmy problemy trzyetapowo:
1) dane i wymagania,
2) warianty,
3) rozwiązanie.
Podejmujmy decyzje inwestycyjne na bazie trzech kryteriów:
1) finanse,
2) parametry wydajnościowe,
3) kryteria niepieniężne.
Wdrażajmy w trzech krokach:
1) koncepcja,
2) projekt detaliczny i przetarg,
3) realizacja.
Aby na koniec móc powiedzieć jak Juliusz Cezar: veni, vidi, vici (przybyłem, zobaczyłem, zwyciężyłem).
Autor artykułu: Jacek Olszewski, Senior Principal, Międzynarodowa Grupa Doradczo-Inżynierska Miebach Consulting
Artykuł ukazał się w wydaniu nr 2/2021 (kwiecień-maj) “Logistics Manager”. Więcej o czasopiśmie TUTAJ
Zobacz również