MAGAZYN
Całkiem nowe oblicze – 30 lat polskiej intralogistyki
O transformacji gospodarczej w Polsce, płaszczyznach, na jakich rozwijała się polska intralogistyka, a także o innowacjach w technologiach magazynowych z ekspertami z firmy Jungheinrich: Danielem Lasoniem, kierownikiem produktu i koordynatorem ds. rozwoju kompetencji, a także Arturem Thomasem, menedżerem projektów systemowych, rozmawia Dominik Jańczak – redaktor naczelny magazynu „Logistics Manager”.
Data publikacji: 08.11.2024
Data aktualizacji: 12.11.2024
Podziel się:
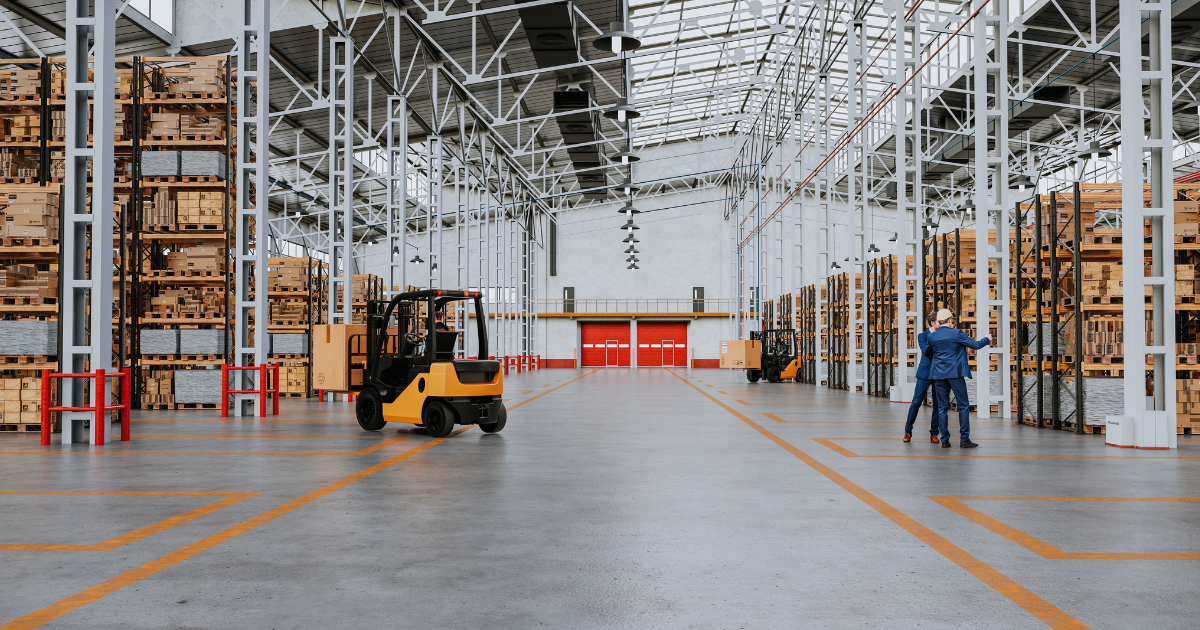
Dominik Jańczak: Jako Jungheinrich od 30 lat aktywnie uczestniczycie w rozwoju branży intralogistycznej w Polsce – jak zmieniła się ona przez ten czas? Czy jesteś w stanie określić kamienie milowe ewolucji polskiej intralogistyki na przestrzeni ostatnich trzech dekad?
Daniel Lasoń: Polska od lat 90. przechodziła transformację gospodarczą, która miała swoje odzwierciedlenie w logistyce. Pierwszy aspekt zmian to kwestie technologiczne. Jest tutaj istotny nie tylko fakt, że silniki prądu stałego zamieniliśmy na silniki prądu zmiennego. Przede wszystkim zmieniło się ogólne podejście do elektroniki. Wraz z rozwojem urządzeń, z których korzystamy na co dzień, takich jak AGD czy telefony komórkowe, zaczęliśmy powszechnie ufać technologii.
Kolejnym kamieniem milowym było pojawienie się technologii litowo-jonowej. Początkowo obserwowaliśmy jej rozwój w niewielkich urządzeniach, takich jak telefony, ale w 2010 r. przebojem wdrała się do intralogistyki, ponieważ wprowadziliśmy pierwszy wózek nią zasilany. To była absolutna rewolucja na rynku logistycznym. Wspomniany rodzaj baterii zmienił zasady eksploatacjii flot wózków widłowych.
Niedługo później pojawiły się zmiany w podejściu do pracy ze sprzętem intralogistycznym. W latach 90. oraz na początku drugiego tysiąclecia ludzie chcieli wszystko obsługiwać samodzielnie. Kluczowa była kontrola. Wiele firm zatrudniało chociażby własnych mechaników do obsługi urządzeń. Z czasem na rynku pojawił się outsourcing różnych usług i okazało się, że organizacje z chęcią oddają to, czego wcześniej kurczowo się trzymały. Dlaczego tak się stało? Wyszło na to, że nikt tak dobrze jak serwis dostawcy wózków nie jest w stanie nimi zarządzać, aby były cały czas dostępne dla klienta. Kolejna kwestia w tym kontekście to fakt, że outsourcing procesów, dostaw czy serwisu okazał się modelem znacznie korzystniejszym finansowo.
Początkowo w intralogistyce dominował też model posiadania, kupowania sprzętu. Jeżeli firma potrzebowała przeładować towar z punktu A do punktu B, bezrefleksyjnie kupowała wózek widłowy. Dziś klienci mają znacznie większą świadomość. Rozumieją. że jest to inwestycja długoterminowa, element wpływający na wynik finansowy danego kontraktu – dlatego dziś częściej mówi się o całkowitych kosztach eksploatacji, a nie tylko o cenie zakupu. Chętniej stawiamy również na użytkowanie czy odnawianie sprzętu.
W ostatnim czasie rośnie także znaczenie aspektów związanych z ochroną środowiska. Zaczynamy rozumieć, że jest to dla nas kwestia zasadnicza. Dlatego też, aby zmniejszyć emisję spalin i nie zatruwać planety, Jungheinrich zrezygnował z wózków spalinowych.
Dzisiaj w obszarze automatyki czy robotyzacji
przechodzimy do zwinnego projektowania
rozwiązań, które tworzymy wspólnie z klientem.
Mają one kolejne iteracje już w trakcie użytkowania.
DJ: Wraz z rozwojem technologii rosła również wydajność naszej pracy, prawda?
DL: Wszystkie rynki, które się rozwijają – widzieliśmy to również u nas w latach 90. – używają prostych urządzeń wielofunkcyjnych, takich jak wózki spalinowe. Kraje rozwinięte przechodzą na wózki techniki magazynowej – na początku wózki elektryczne, z czasem te wysokiego składowania. W każdym razie klienci z czasem dochodzą do wdrażania urządzeń systemowych albo pełnej automatyzacji. W latach 90. dominowała ręczna praca magazynowa z wykorzystaniem wózków spalinowych. Powodowało to oczywiście niskie standardy magazynowania i niewielkie wpływy IT w logistyce. Później przyszło nowe tysiąclecie, wdrożono pierwsze WMS-y. Do magazynów weszły więc komputery. To był moment, w którym gdzieniegdzie zaczęło tlić się zainteresowanie automatyką. Wzrastało też zaufanie do technologii, o czym już wspominałem. Wózki kupowane do magazynu nie musiały być już najprostsze, aby klient był w stanie samodzielnie je naprawić. Technologie przyspieszyły, zwiększając wydajność pracy, a co za tym idzie – rentowność polskich biznesów.
Na naszym rynku pojawiło się też sporo niemieckich firm, od których uczyliśmy się kultury zarządzania. Polska weszła do Unii Europejskiej i otrzymała ogromne dofinansowania, dzięki czemu mogliśmy pozwolić sobie na inwestycje. Wraz z gospodarką rozwinęła się też logistyka. Systematycznie spadało znaczenie wózków spalinowych, których w Jungheinrich już wtedy właściwie nie sprzedawaliśmy. Rosło z kolei zapotrzebowanie na wózki techniki magazynowej.
Od 2010 r. obok kwestii wydajności coraz częściej zaczęto zwracać uwagę na bezpieczeństwo. To stymulowało rozwój rozwiązań do zarządzania flotą czy innych systemów powodujących, że praca wózków na magazynie jest bezpieczniejsza. Pojawiło się oprogramowanie i elektronika pozwalające na kontrolowanie i nadzorowanie bezpieczeństwa flot. To wszystko wpisywało się w takie koncepty, jak Industry 4.0 czy Smart Warehouse. Aktualnie znajdujemy się w momencie, w którym nie sam sprzęt jest oczkiem w głowie naszego klienta, ale cały ekosystem IT zbudowany wokół danego narzędzia, takiego jak wózek widłowy.
Chcąc podsumować to 30 lat, można powiedzieć, że przeszliśmy od ręcznej pracy z towarami do automatyzowania procesów. Proces tej zmiany był długi, a jego obserwowanie naprawdę fascynujące. Intralogistyka zmieniła się nie do poznania. Choć tutaj warto dodać, że zarysowana przed chwilą linia czasowa dla każdego przedsiębiorstwa mogła wyglądać nieco inaczej. Niektóre firmy nadal są na którymś etapie tej drogi.
Artur Thomas: Dołączyłem do firmy Jungheinrich w 2008 r. Był to bardzo ciekawy okres, o którym padło tutaj już kilka słów. Zagraniczne koncerny przynosiły do nas swoje know-how, całkowicie zmieniając reguły gry. Dość wspomnieć o Lidlu czy Amazonie. Wtedy najprostsze rozwiązania, takie jak wózki spalinowe, zaczęły schodzić na dalszy plan. Trudno uwierzyć, że ten czas tak szybko ucieka i przeszliśmy tak długą drogę. Po 2010 r. pojawiły się pierwsze hasła związane z cyfryzacją i zrównoważonym rozwojem. Zaczęliśmy dbać o ekologię i efektywność energetyczną. Kilka lat później pojawiły się inteligentne magazyny i naprawdę zaawansowane technologie… aż przyszedł rok 2020 – całkowita zmiana okoliczności gospodarczych, pandemia i zerwane łańcuchy dostaw.
DJ: Zakładam, że wraz ze zmianami społeczno-gospodarczymi zmieniało się Wasze portfolio produktowe?
AT: Zdecydowanie. Moje pierwsze szkolenia z wózków widłowych polegały na tym, że opowiadano mi o przewagach katalizatora trójdrożnego nad dwudrożnym i o możliwościach zastosowania wózków spalinowych w magazynie. Drukowany katalog produktowy był wtedy zdominowany przez rozwiązania spalinowe właśnie. Nie dość, że teraz tego typu materiałów nie drukujemy już prawie wcale, chcąc oszczędzać lasy, to w naszej gamie produktowej trudno znaleźć proste rozwiązania spalinowe. Dominują w niej produkty elektryczne jako te bardziej uniwersalne oraz rozwiązania specjalistyczne, systemowe – związane z automatyką, robotyką i systemami IT.
Oprócz transformacji portfolio produktowego zmienił się również sposób obsługi naszych klientów. Przeszliśmy od modelu sprzedaży akwizycyjnej do doradczej, a teraz realizujemy przekrojowe projekty. Tworzymy wyspecjalizowane zespoły, które holistycznie podchodzą do wyzwań naszych partnerów biznesowych i rekomendują nie konkretny produkt, ale kompleksowe wsparcie zależne od specyfiki procesów klienta – od analizy wymagań, przez konsultacje i propozycje rozwiązań z zakresu WMS, po wózki widłowe z odpowiednim źródłem energii.
DJ: Skoro mamy za sobą takie zmiany, to czy rewolucja w intralogistyce jest jeszcze możliwa? Czy nadal możemy dziś mówić o innowacjach w obszarze magazynowania?
AT: Szczerze mówiąc, wolałbym termin „ewolucja”, ponieważ zmiany, o których rozmawiamy, miały raczej płynny charakter. I takie też wdrożenia rekomendujemy zwykle naszym klientom. Przykład z zakresu transportu bliskiego w obiekcie – kiedy rozpoczynamy pracę z nowym partnerem, zawsze wymieniamy wózki w jego magazynie pojedynczo. Nie zastępujemy od razu całej floty, żeby nie narażać klienta na niepotrzebny szok procesowy. Płynne przejście od jednego stanu rzeczy do drugiego jest zdecydowanie dużo bardziej korzystne dla organizacji.
Natomiast jeśli chodzi o innowacje w magazynach i o to, czy są jeszcze możliwe? Zdecydowanie. Kiedy rozpoczynałem pracę w branży, wyznacznikiem nowych generacji w wózkach systemowych był okres siedmioletni. Szczerze mówiąc, przez długi czas traktowałem to jako stan zastany i taki, który będzie trwał wiecznie. Dzisiaj w obszarze automatyki czy robotyzacji przechodzimy do zwinnego projektowania rozwiązań, które tworzymy wspólnie z klientem. Mają one kolejne iteracje już w trakcie użytkowania. Jednak pozwalają na to, aby proces logistyczny czy produkcyjny był dużo bardziej odporny na warunki zewnętrzne, takie jak sytuacja geopolityczna czy dostępność rąk do pracy. W podobny sposób, maksymalizując wartość dla klienta, chcemy wykorzystywać analizę danych, uczenie maszynowe czy sztuczną inteligencję.
Dziś wózek po uruchomieniu przeprowadza własną autodiagnostykę. Zasypują nas ciągi informacji, a żeby efektywnie nimi zarządzać i mieć pełny obraz sytuacji, potrzebujemy kolejnych technologii. Spójrzmy chociażby na magazyny – WMS-y czy WES-y pomagają nam zobaczyć z lotu ptaka, co dzieje się w obiekcie, a także na podstawie terabajtów danych płynących przez nasz ekosystem podjąć trafną decyzję biznesową.
Oprócz tego wspomniałbym w tym kontekście o wirtualnej i rozszerzonej rzeczywistości. która już w tej chwili zaczyna wspierać nas w szkoleniach i serwisowaniu urządzeń. Wystarczy wyobrazić sobie sytuację, w której doświadczony technik zakłada okulary i jest w stanie zdalnie wesprzeć drugą osobę, będącą gdzieś w zupełnie innym miejscu na świecie, w czasie rzeczywistym. Potencjał na rozwój wykazuje również obecny już od kilku lat internet rzeczy. Mamy zatem sporo ciekawych obszarów, które mogą nas jeszcze zaskoczyć. A wszystko po to, abyśmy mogli redukować koszty, poprawiać jakość, lepiej zarządzać zapasami i dopasowywać się do tego, czego wymaga dynamiczna sytuacja rynkowa.
DL: W pełni się zgadzam. W tego typu technologiach na ogół będziemy mówić o ewolucji. Spójrzmy chociażby na powstanie internetu. Mogłoby się wydawać, że pod koniec lat 90., kiedy ludzie otrzymali do niego dostęp, była to istna rewolucja. Ale należy pamiętać, że na początku użytkowników nie mieliśmy zbyt wielu – ich liczba przyrastała w czasie. Był to zatem proces, który miał swój konkretny początek, ale nie trwał jeden dzień.
Wracając do technologii logistycznych, na początku lat 90. mieliśmy w ofercie system ISM Online pozwalający kontrolować wózki widłowe. Ale nikt go wtedy nie chciał, sprzedawaliśmy pojedyncze sztuki. W pewnym momencie nastąpiło odwrócenie trendu i stopniowa zmiana podejścia do tego typu rozwiązań. Trzy dekady później około 70% flot ma już FMS-a. Z punktu widzenia całego stulecia możemy zatem mówić o pewnej rewolucji, radykalnym przyspieszeniu. Ale z perspektywy tych 30 lat zmiana była ewolucyjna.
Kiedy powiemy naszemu operatorowi, że od jutra jeździ nowym wózkiem elektrycznym, to dla niego będzie to rewolucja. Sprzęt z systemem zone control po wjechaniu na konkretny obszar magazynu zareaguje w zaprogramowany sposób, np. zmniejszy prędkość czy włączy oświetlenie. Jeśli wcześniej operator działał bez takich rozwiązań, sposób jego pracy siłą rzeczy stanie na głowie. Także kwestię „rewolucja czy ewolucja” możemy rozpatrywać z różnych perspektyw.
Wracającąc do pytania o innowacyjność… Myślę, że w magazynach możemy spotkać sporo innowacji rozumianych jako nowe rozwiązania w obrębie dostępnych technologii. Chociażby systemy nadzorowania ładowania baterii. Badają one, czy sieć nie jest przeciążona, co powoduje większe pobory energii, a także sprawdzają, czy wózki są maksymalnie dostępne. Inny przykład – rozpoznawanie pieszych. Cyftowa kamera widzi, co dzieje się w danym obszarze. Jeżeli zobaczy osobę zmierzającą w kierunku jadącego wózka, zarówno człowiek, jak i maszyna otrzyma monit z tym związany. Nie muszą się wzajemnie widzieć – ostrzeże ich system IT.
Zaawansowane systemy nie tylko radykalnie wspierają operatorów w magazynie, ale mają też znaczenie dla bezpieczeństwa w obiekcie. Nie mówiąc już o tym, że wpływają na wydajność i zmniejszają koszty eksploatacji, np. poprzez unikanie wypadków czy innych zdarzeń niepożądanych. Widzimy, że klienci coraz bardziej cenią kwestie bezpieczeństwa – to podejście zmieniło się bardzo mocno na przestrzeni 30 lat.
Oprócz tego ewoluowało również podejście do pracownika. Coraz więcej firm zwraca uwagę na to, co mówią o nich operatorzy wózków widłowych czy inni członkowie zespołu. To dla nich istotne, aby nie odstawać technologicznie od konkurencji – czyli w jednej firmie operator jeździ na regularnie psującym się sprzęcie, a w innej ma wózek z klimatyzacją i supersiedzeniami. Rotacja pracowników kosztuje, dlatego przedsiębiorcy chcą ich zatrzymać u siebie poprzez większą ergonomię, komfort i bezpieczeństwo pracy.
AT: Żyjemy w czasach, kiedy informacja o tym, jakie rozwiązania stosujemy czy jakim pracodawcą jesteśmy, może mieć ogromne zasięgi – głównie dzięki social mediom. To już nie kwestia lokalna, o której szepczą między sobą pracownicy z danej dzielnicy. Zależy nam, aby dobre praktyki i ciekawe wdrożenia trafiały do jak największej liczby zainteresowanych odbiorców. Dlatego też Jungheinrich od jakiegoś czasu dość mocno angażuje się w realizację materiałów referencyjnych. Razem z naszymi klientami prezentujemy, co udało nam się razem zrobić oraz opowiadamy, jakie korzyści przynoszą wypracowane i wdrożone rozwiązania.
DJ: A baterie litowo-jonowe to jeszcze innowacja?
DL: To technologia, która miała pewne znamiona rewolucji, o którą wcześniej pytałeś. Odejście od rozwiązań kwasowych nastąpiło bardzo szybko. W ciągu dekady miały miejsce radykalne zmiany. Baterie litowo-jonowe pojawiły się w Europie w 2010 r., a w Polsce wprowadzaliśmy je w 2018 r. Dziś już ponad 65% wózków sprzedawanych przez Jungheinricha wyposażonych jest w ten rodzaj zasilania. Pierwsze kroki były dość niepewne – musieliśmy obalić kilka fałszywych narracji, głównie związanych z bezpieczeństwem i awaryjnością. Dziś branża rozumie, że wspomniana technologia zmieniła rynek na lepsze, będąc stabilnym, bezpiecznym i dającym przestrzeń na optymalizację rozwiązaniem.
DJ: Dziękuję za pierwszą część rozmowy. Będziemy ją kontynuowali w kolejnym wydaniu „Logistics Managera”, gdzie porozmawiamy o najnowszych rozwiązaniach w gamie modelowej firmy Jungheinrich.
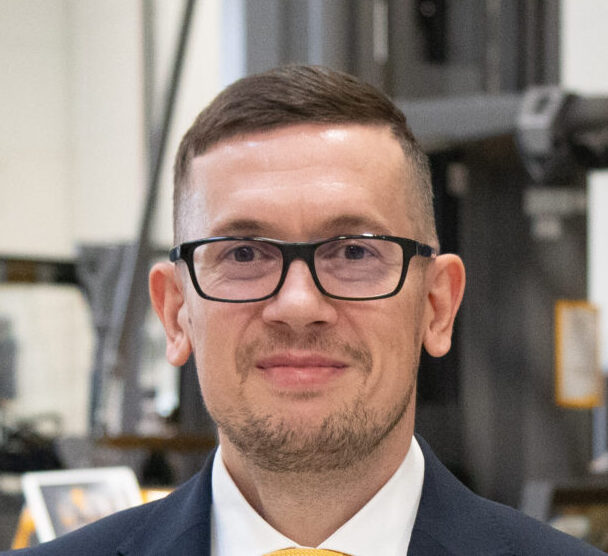
Artur Thomas
Menedżer projektów systemowych
Jungheinrich Polska
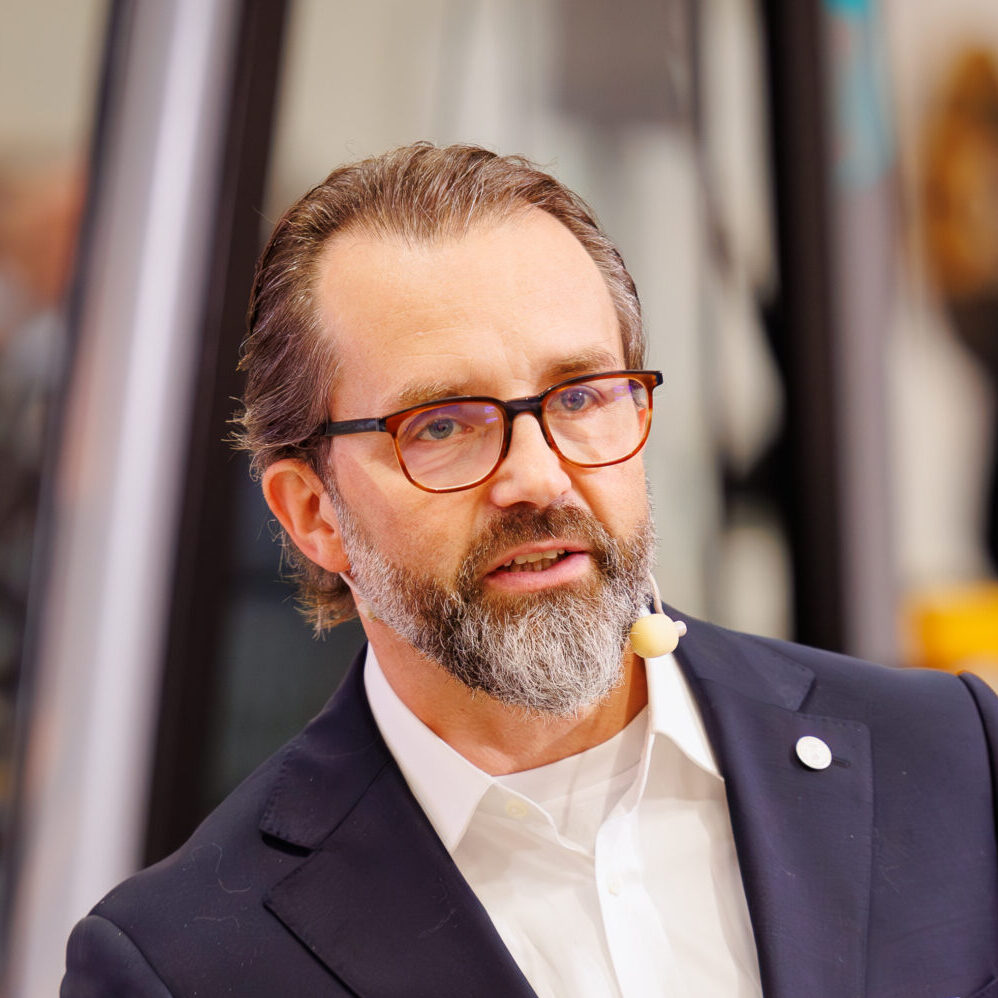
Daniel Lasoń
Kierownik produktu i koordynator ds. rozwoju kompetencji
Jungheinrich
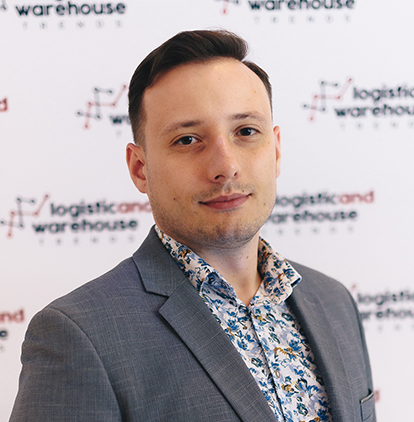
Dominik Jańczak
Redaktor naczelny „Logistics Manager”
MPF
Zna rynek wydawniczy od podszewki. Pracował w redakcjach takich magazynów branżowych jak „Flota” czy „MŚP Biznes”. Zaprojektował tysiące stron książek i magazynów, wprowadził na rynek kilkanaście produktów wydawniczych. Autor koncepcji outsourcingu wydawniczego, która skraca czas przygotowania materiałów do druku. Pisze artykuły eksperckie na LinkedInie oraz publikuje w mediach branżowych. Prywatnie gitarzysta, pasjonat publikacji elektronicznych oraz nowych mediów.
Zobacz również