MAGAZYN
Inteligentne okulary, smartwache i… egzoszkielety - ubieralne technologie w polskich magazynach
Nikt nie chce dziś wykonywać uciążliwych prac, wymagających wielkiego wysiłku fizycznego. Dlatego świadomi przedsiębiorcy starają się wprowadzać różne rozwiązania pomagające albo usprawniające wykonywanie najcięższych obowiązków, m.in. w halach fabrycznych i magazynach. Dzięki niesłychanie szybkiemu rozwojowi technologii takich ułatwień jest coraz więcej.
Data publikacji: 20.11.2023
Data aktualizacji: 21.11.2023
Podziel się:
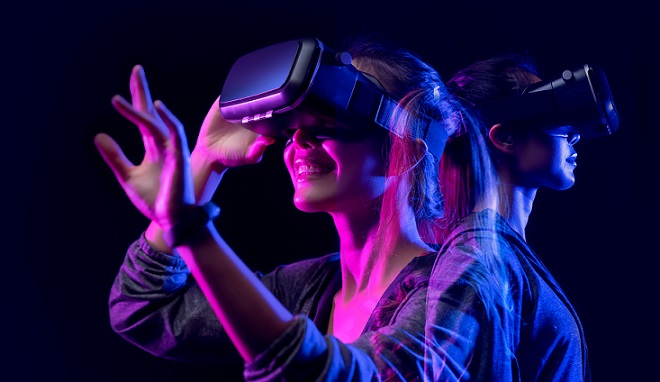
Według badania „Global Warehousing Vision Study 2023” aż 73% decydentów magazynowych mówi, że ważne jest dla nich wdrażanie przystępnych i intuicyjnych w obsłudze urządzeń. Ten sam odsetek twierdzi, iż priorytet branży stanowi implementacja nowych technologii. Dostępne obecnie urządzenia odpowiadają na te potrzeby.
Pracodawca godny zaufania
– Jako jedna z największych sieci handlowych w Polsce, posiadając ponad 3400 sklepów, stale usprawniamy proces logistyczny konieczny do zapewnienia właściwej obsługi wszystkich placówek – mówi Małgorzata Makar, menedżer ds. logistyki w sieci Biedronka. – Jednym z filarów strategii zrównoważonego rozwoju sieci jest zrównoważony łańcuch dostaw. Do naszych codziennych wyzwań należy dostarczanie świeżych produktów dla ponad 5 milionów klientów, którzy każdego dnia odwiedzają nasze sklepy. W realizacji tego założenia pomagają nam nowoczesne centra dystrybucyjne. Jest ich 17, a pracę znajduje w nich 8700 osób, co stanowi ponad 10% całkowitego zatrudnienia organizacji. W doskonaleniu procesów operacyjnych oraz w zarządzaniu logistyką stawiamy na nowoczesne technologie i automatyzację, dlatego stosujemy rozmaite urządzenia wpływające na poprawę efektywności, m.in. tak zwane wearables, czyli urządzenia ubieralne. Wdrażamy procesy automatyzacji, tworząc nowoczesne i bezpieczne miejsca pracy, co stanowi kluczowy element bycia pracodawcą godnym zaufania.
Pracownicy centrów dystrybucyjnych Biedronki korzystają na co dzień z technologii Voice Picking. To system kompletacji głosowej, dzięki któremu pracownik nie wykonuje takich czynności systemowych, jak odczytywanie i potwierdzanie zamówień. Każda osoba wyposażona jest w terminal, który obsługuje głosowo za pomocą systemu słuchawkowego, dlatego może być w pełni skupiona na głównym zadaniu, czyli kompletacji zamówień bez konieczności manualnego zatwierdzania ich na terminalach. Informacje o zamówieniach są importowane z systemu i przetwarzane w dźwięk, czyli precyzyjne instrukcje dla pracowników potrzebne do przygotowania towaru. Obsługa jest bardzo łatwa i intuicyjna, a dzięki zastosowaniu takich urządzeń pracownicy mają zapewnione optymalne warunki pracy.
Rozwiązanie jest sukcesywnie wdrażane od 2018 r. Po tych kilkuletnich doświadczeniach można potwierdzić, że ma pozytywny wpływ na wzrost produktywności pracowników. Minimalizuje także liczbę błędów, co naturalnie wiąże się z ogromną oszczędnością czasu.
Większa efektywność
Podobnie grupa Żabka stale poszukuje rozwiązań, które pozwalają rozwijać sieć sklepów, a także ułatwiają i usprawniają codzienne zadania pracownikom. Chodzi o automatyzację, sztuczną inteligencję czy urządzenia z kategorii wearables. Jednym z obszarów, w którym znajdują one zastosowanie na coraz większą skalę, są procesy związane z logistyką.
– Dobrym przykładem jest znajdujące się nieopodal Radzymina centrum logistyczne, otwarte w czerwcu tego roku – informuje Arkadiusz Nowicki, dyrektor operacji logistycznych w Grupie Żabka. – Na powierzchni 60 tysięcy m2 został umiejscowiony m.in. automatyczny magazyn wysokiego składowania (High-Bay). Znajdują się tam także komory chłodni i mroźni w pięciu różnych strefach temperaturowych (od –24 °C do +20 °C). Na całej powierzchni magazynowej zaimplementowano automatyczny system transportu wewnętrznego. W kontekście urządzeń wearables wykorzystujemy Voice Picking, czyli kompletację głosową opartą o system zestawu słuchawkowego sterowanego głosem, połączonego z zakładanym na dłoń skanerem. Rozwiązanie zostało wdrożone w przestrzeniach, gdzie przechowywane są produkty mrożone i te wymagające chłodzenia. Wspiera pracowników w czasie kompletowania asortymentu znajdującego się w magazynie.
Voice Picking uwalnia od ciągłego spoglądania na ekran lub papierowe dokumenty stosowane w standardowych procesach kompletacyjnych. Zastosowany w tym rozwiązaniu skaner naręczny jest obsługiwany jedynie kciukiem. Przed rozpoczęciem procesu kompletacji asortymentu pracownik otrzymuje zaimportowane z systemu zarządzania magazynem zamówienia, które przekazuje mu się w formie dźwiękowej. Wprowadzane są proste i zrozumiałe komunikaty głosowe kierujące pracowników kompletacji do konkretnych lokalizacji, przy jednoczesnym określeniu ilości i rodzaju kompletowanego asortymentu. Zakończenie kompletacji danej linii zamówienia odbywa się poprzez skanowanie lokalizacji oraz kodu kreskowego produktu.
Wdrożenie tego rozwiązania dało realne korzyści zarówno firmie, jak i członkom zespołu. Przez fakt, że pracownik rzadziej musi zerkać na ekran, nastąpił wzrost wydajności, a to doprowadziło do optymalizacji czasu oraz tempa pracy. System zminimalizował też ryzyko wystąpienia błędu, co wpłynęło m.in. na zwiększenie dokładności kompletacji, poprawę zgodności stanów magazynowych oraz dostępność produktów. To wszystko przekłada się ostatecznie na zadowolenie klientów.
– Grupa Żabka już teraz wyznacza trendy w swojej branży w aspekcie wdrażania nowych technologii – twierdzi Arkadiusz Nowicki. – Jednak stale dążymy do tego, by jeszcze szybciej i efektywniej odpowiadać na potrzeby klientów i zmieniającego się otoczenia gospodarczego. Z tego powodu nieustannie jednym z naszych priorytetów jest poszukiwanie i wdrażanie rozwiązań technologicznych, które zwiększają efektywność wykorzystywanych przez nas zasobów, a także minimalizują wpływ naszej działalności na planetę.
Egoszkielety to lekkie, pozbawione elektroniki, funkcjonalne, odporne na kurz i wodę skuteczne konstrukcje, które pracownicy mogą traktować jako dodatkowe ubranie ochronne
Mniej błędów
– W dobie cyfrowych innowacji firmy na całym świecie odkrywają nowe sposoby wykorzystywania technologii w praktyce – przypomina Jarosław Kurosz, dyrektor produkcji w zakładzie Volkswagena we Wrześni. – Nasze fabryki w Polsce stoją na czele tej rewolucji, wykorzystując rzeczywistość rozszerzoną (AR) w procesach produkcyjnych. Kluczem do sukcesu stało się wprowadzenie okularów Hololens. Dzięki nim pracownicy mogą przejść przez najbardziej złożone procedury, otrzymując wizualne wsparcie wyświetlane bezpośrednio przed ich oczami. Oznacza to ścisłe zachowywanie standardów, mniej błędów, a w efekcie większą efektywność.
Innym przełomowym narzędziem stały się dla nas okulary GoogleGlass. Kiedy pojawia się problem, którego rozwiązanie nie jest oczywiste, operator może błyskawicznie skonsultować się z ekspertem, udostępniając mu obraz na żywo. To tak, jakby mieć przy sobie specjalistę gotowego pomóc w każdej chwili.
– Gdy myślimy o smartwatchach, zwykle wyobrażamy je sobie jako modne dodatki do monitorowania naszej aktywności fizycznej czy powiadomień z telefonu – zwraca uwagę Jarosław Kurosz. – Jednak w naszych zakładach te niewielkie urządzenia odgrywają znacznie ważniejszą rolę. Rewolucjonizują procesy produkcyjne. W fabryce samochodów każda sekunda ma realne znaczenie i przekłada się na końcowy wynik.
Za sprawą innowacyjnych strategii wprowadzanych od 2018 r. smartwatche stały się integralną częścią linii produkcyjnych w ramach inicjatywy Przemysł 4.0. To, co rozpoczęło się jako sposób na poprawę komunikacji między urządzeniami a ich operatorami, szybko usprawniło produkcję. Dzięki temu zakłócenia techniczne są identyfikowane i rozwiązywane znacznie szybciej, co przekłada się na imponujące zwiększenie wydajności – nawet o trzy karoserie dziennie.
Będąc narzędziami komunikacji, smartwatche umożliwiają operatorom linii produkcyjnych bieżący podgląd na to, co dzieje się na ich obszarze. Gdy pojawia się jakiekolwiek zakłócenie, pracownik jest o tym fakcie natychmiast informowany i może podjąć odpowiednie działania.
Technologia ta została zaimplementowana w smartfonach pracowników utrzymania ruchu. W przypadku awarii operator linii produkcyjnej może więc szybko wezwać odpowiednią służbę. Wspomagające funkcje w telefonie, takie jak skanowanie kodów QR, zdalne zamawianie części z magazynu czy dostęp do dokumentacji technicznej dodatkowo przyspieszają i usprawniają procesy podczas usuwania awarii.
Drabina korzyści
– Lubimy komfort i wybieramy produkty przyjemne w obsłudze – twierdzi Jacek Żurowski, dyrektor regionalny w firmie Zebra Technologies. – Już nie tylko na rynku konsumenckim. Cieszę się, że ten trend zawitał również do przestrzeni logistycznej i magazynowej. Patrząc na korzyści użytkowników, można je przedstawić w postaci swoistej drabiny. Pierwszy szczebel to zadowolenie pracowników z szybkiej nauki obsługi sprzętu. Drugi oznacza lepszy monitoring zasobów i możliwość unikania przerw w łańcuchach dostaw. Przedsiębiorca jest w stanie dobrze przewidzieć, jakie zamówienia musi złożyć, aby zapewnić sobie stabilność. Jak pokazuje badanie „Warehouse Vision Study”, 82% osób decyzyjnych przyznaje, że lepsza widoczność operacyjna oznacza możliwość zautomatyzowania większej liczby decyzji w celu lepszego wykorzystania personelu i zasobów.
Kolejny szczebel to szybkość realizacji tych zamówień, przy których pracują sprawnie działający pracownicy. Jest to szczególnie ważne w e-commerce. Sklepy, mając podobną ofertę, konkurują jakością i szybkością obsługi. Ogromne znaczenie ma też dostęp do serwisu. Najważniejszy dla przedsiębiorcy punkt to oczywiście korzyść finansowa wynikająca ze wszystkich pozostałych elementów procesu.
Zebra oferuje kompleksową gamę produktów zarządzania magazynami. Chodzi o rozmaite urządzenia: od czytników kodów kreskowych, poprzez rozwiązania w zakresie technologii RFID, czujniki środowiskowe, do komputerów mobilnych i nasobnych. Obecnie zauważa się coraz większe zainteresowanie branży przede wszystkim sprzętem RFID. Jak wynika z cytowanego już badania, 94% europejskich decydentów z branży logistyki magazynowej (91% na całym świecie) spodziewa się wykorzystania technologii RFID w celu zwiększenia kontroli nad łańcuchem dostaw w ciągu najbliższych pięciu lat.
To rozwiązanie umożliwia odczyt i zapis informacji oraz możliwość lokalizowania tagów w przestrzeni dzięki falom radiowym. Mowa o całym systemie danych stworzonym na fundamencie przesyłu treści. Istnieją czytniki RFID i tagi RFID, które można umieszczać na dowolnych obiektach – praktycznie na wszystkim. Do systemu RFID wliczają się również anteny i drukarki tagów oraz oprogramowanie obsługujące tę sieć połączonych ze sobą w magazynie punktów. Korzystając z cyfrowego systemu zarządzania magazynem Zebry, klient jest w stanie monitorować stan swoich zasobów łącznie z analizą miejsca, w jakiej znajdują się zapasy, liczbą tych przedmiotów, a nawet temperaturą i poziomem wilgotności, co przydatne jest szczególnie w przemyśle farmaceutycznym.
Do najważniejszych funkcji technologii magazynowych należy monitoring. Oprogramowanie, na jakim pracuje sprzęt Zebry, a także łączenie się produktów z chmurą zapewnia bieżącą kontrolę nad stanem magazynowym i możliwość bardzo szybkiego reagowania na potrzeby uzupełniania zasobów. A przecież z roku na rok coraz więcej osób zarządzających w branży magazynowej stawia na automatyzację i wygodę zatrudnionych.
Pracowników pierwszej linii można wyposażyć w przenośne drukarki kodów kreskowych przyczepiane do paska, które eliminują potrzebę nieustannego poruszania się w przestrzeni magazynowej. Audytorzy mają do dyspozycji proste w obsłudze czytniki kodów kreskowych, w tym skanery pierścieniowe umożliwiające pracę obiema wolnymi rękami. Największą korzyścią dla pracowników jest więc wygoda użytkowania i ograniczenie frustracji z powodu wadliwego sprzętu.
Będąc narzędziami komunikacji, smartwatche umożliwiają operatorom linii produkcyjnych bieżący podgląd na to, co dzieje się na ich obszarze. Gdy pojawia się jakiekolwiek zakłócenie, pracownik jest o tym fakcie natychmiast informowany i może podjąć odpowiednie działania.
Blaski…
Oddzielną kategorię sprzętu stanowią tak zwane egzoszkielety. Popularnie mówiąc, chodzi o rodzaj „zbroi”, która pomaga wykonywać najcięższe prace, przede wszystkim podnosić i przenosić ciężary. Wspomniane rozwiązanie jest stosunkowo nowe, zatem dopiero zdobywa sobie popularność.
Nasz naturalny szkielet jest szkieletem wewnętrznym (endoszkieletem), który przenosi na podłoże obciążenia związane z podnoszeniem i przenoszeniem przedmiotów – wyjaśnia dr hab. inż. Andrzej Grabowski, prof. Centralnego Instytutu Ochrony Pracy – Państwowego Instytutu Badawczego w miesięczniku „Bezpieczeństwo pracy – nauka i praktyka”. – Wymagania stawiane w pracy odbiegają od warunków naturalnych, co sprawia, że obciążenie układu mięśniowo-szkieletowego w trakcie wykonywania prac fizycznych może doprowadzić do powstania zaburzeń w jego funkcjonowaniu. Rozwiązaniem może być zastosowanie dodatkowego, zewnętrznego szkieletu (egzoszkieletu) odciążającego – w mniejszym lub większym stopniu – zarówno nasz wewnętrzny szkielet, jak i mięśnie.
Najprostszym rozwiązaniem jest zastosowanie egzoszkieletu pasywnego, np. do kończyn dolnych, ułatwiającego przenoszenie ciężkich plecaków (nawet 50 kg ładunku). Stelaż plecaka przymocowany jest do górnej części egzoszkieletu znajdującej się na wysokości pasa, a jego ciężar zostaje przeniesiony przez konstrukcję egzoszkieletu na podłoże. Dodatkowo taki szkielet zewnętrzny może być wyposażony w pneumatyczne siłowniki w stawie kolanowym. W trakcie kucania ciśnienie znacząco wzrasta, a jego nacisk na tłok siłownika pomaga przy ponownym wyprostowaniu.
Tego typu egzoszkielety są stosowane najczęściej przez żołnierzy, natomiast w przemyśle bardziej przydają się do odciążania górnej części ciała. Najczęściej rozważane są egzoszkielety odciążające kręgosłup (np. przenoszące obciążenie związane z przemieszczeniem przedmiotu bezpośrednio na biodra lub kończyny dolne) i kończyny górne, wspomagające np. długotrwałe prace wykonywane ponad głową (konstrukcja egzoszkieletu stabilizuje się w wybranym położeniu, dzięki czemu pracownik nie musi podtrzymywać ciężaru swojej ręki oraz trzymanego narzędzia) – np. do zastosowania w przemyśle motoryzacyjnym.
Oczywistą różnicą pomiędzy egzoszkieletem pasywnym a aktywnym jest to, że ten drugi został wyposażony w zestaw siłowników (najczęściej wykorzystuje się silniki elektryczne) pozwalających na zwiększenie możliwości pracownika w zakresie podnoszenia przedmiotów. Siłowniki mogą pełnić rolę wspomagającą (tzn. do podnoszenia ciężaru wykorzystywana jest zarówno siła ludzkich mięśni, jak i egzoszkielet) oraz całkowicie odciążać człowieka (wtedy podnoszony przedmiot utrzymywany jest w górze tylko i wyłącznie przez egzoszkielet). To drugie rozwiązanie stosuje się zwykle w cięższych konstrukcjach, będących egzoszkieletami całego ciała – zarówno kończyn górnych, jak i dolnych (obciążenie związane z trzymaniem przedmiotu przeniesione zostaje na podłoże przez konstrukcję egzoszkieletu). Mniej oczywiste jest to, że egzoszkielet aktywny musi być wyposażony w system sterowania oraz zestaw zabezpieczeń chroniących pracownika przed niewłaściwym działaniem siłowników. Z tego powodu egzoszkielet jest też często nazywany robotem noszonym (ang. wearable robot).
– Egzoszkielet pasywny to sprzęt, który powoduje, że pracownik może się poczuć niczym Iron Man – zauważa Mariusz Żabicki, specjalista ds. marketingu internetowego i e-commerce w firmie Technomex, która jest dostawcą omawianych rozwiązań. – Gdyby BHP było dyscypliną sportową, egzoszkielety pasywne redukujące konieczność używania maksymalnych sił mięśniowych oraz zwiększające wytrzymałość i ochronę przed urazami mogłyby być potraktowane jako legalny doping. To rozwiązanie, które czerpie z doświadczeń firm zajmujących się tworzeniem sprzętu rehabilitacyjnego.
Jego zadaniem jest odciążanie pracownika, co przekłada się na wzrost bezpieczeństwa, wydajności i zdrowia. Ponadto zmniejszenie zmęczenia, a także wyeliminowanie związanych z pracą urazów szyi, ramion i pleców. To również – bez wątpienia – gwarancja większego zadowolenia i rentowności pracodawcy.
Egoszkielety to lekkie, pozbawione elektroniki, funkcjonalne, odporne na kurz i wodę skuteczne konstrukcje, które pracownicy mogą traktować jako dodatkowe ubranie ochronne. Obniżają koszty, absencję pracowników i liczbę urazów. Poprawiają ergonomię, jakość pracy oraz produktywność (nawet o 200–300%).
– Mimo że egzoszkielety pasywne to relatywnie młody sprzęt, zyskał już swoich zwolenników na całym świecie – podkreśla Mariusz Żabicki. – Dzięki zastosowaniu egzoszkieletów Ford Motor Company zaobserwował 83-proc. spadek liczby urazów pracowników, a brytyjska firma Forterra odnotowała redukcję skarg pracowników i zwiększenie o około 25% ich wydajności.
W rozmaitych raportach czytamy: „wyniki badań laboratoryjnych wykazały, że urządzenie zmniejsza wykorzystanie siły mięśni nawet o 20% podczas dźwigania przedmiotów i o 40% podczas pochylania się (…). Korzyści szybko stały się oczywiste. Nasi pracownicy są wspomagani podczas przenoszenia cięższych ładunków, a także mają zapewnioną zewnętrzną stabilizację ciała. Zapobiega to nadmiernemu wysiłkowi i ogranicza ryzyko kontuzji. Dodatkową zaletą urządzeń jest łatwość obsługi, co sprawiło, że testerzy zaakceptowali je w mgnieniu oka (…).” Niektóre z nich skupiają się na ochronie pleców i stawów osób, które wykonując swoją pracę, zmuszone są do dźwigania sporych ciężarów. Taki egzoszkielet potrafi zdjąć z dolnego odcinka pleców obciążenia rzędu 15 kg, co znacznie poprawia komfort pracy i chroni kręgosłup przed kontuzją. Inna wersja urządzenia sprawia, że pracownik może bez problemu udźwignąć ciężar ważący 50 kg. Egzoszkielety wyposażone są w komputery, które bacznie monitorują ruchy użytkownika, wspomagając go adekwatnie do wykonywanej czynności przy pomocy wbudowanych w maszynę silników.
…i cienie
To rozwiązanie ma jednak również sporo przeciwników. W naszym kraju egzoszkielety nie zdobyły jeszcze wielkiej popularności. Nie ma precyzyjnych badań na temat ich wykorzystania. W firmach je dostarczających mówi się o dziesiątkach, a nie tysiącach sztuk. I to raczej o wypożyczaniu, a nie sprzedaży
Po okresie próbnym pracownicy dwóch koncernów motoryzacyjnych skarżyli się, że są one niewygodne. Przedstawiciele prosili o nieujawnianie ich nazw i nie chcieli rozmawiać o szczegółach. Czy w grę wchodzi bariera psychologiczna, czy raczej brak edukacji? A może przyczyna tkwi jeszcze gdzieś indziej?
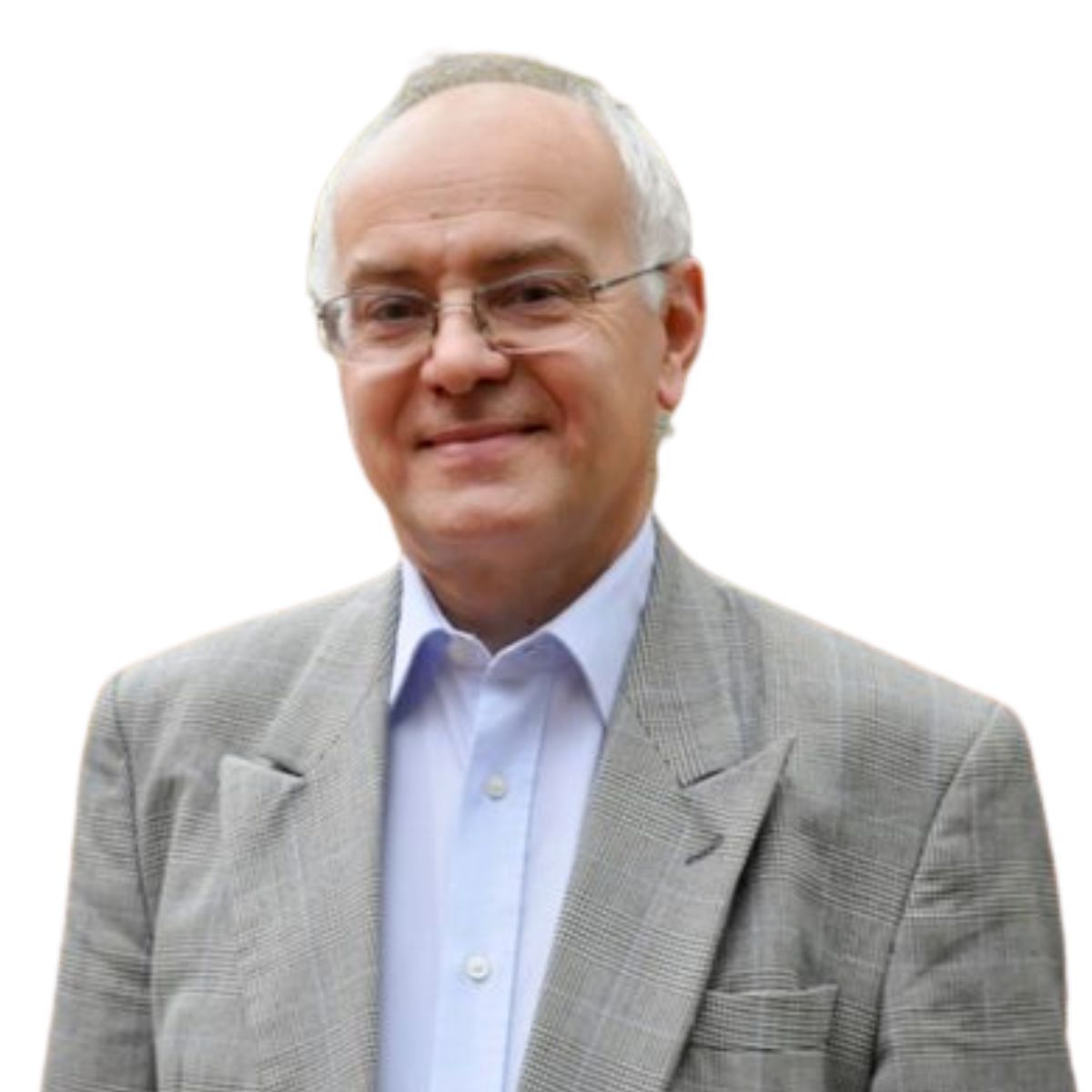
Mieczysław Starkowski
Autor jest dziennikarzem, publicystą, redaktorem magazynu „IT Reseller”. Od wielu lat zajmuje się teleinformatyką, m.in. był redaktorem naczelnym miesięcznika „Świat Telekomunikacji”. Ma wykształcenie ekonomiczne, w przeszłości pracował również w czasopismach biznesowych.
Zobacz również