INTELIGENTNE TECHNOLOGIE
Ile kosztuje dziś automatyzacja magazynu?
Proste pytanie nie zawsze oznacza prostą odpowiedź. Tak jest również w przypadku kwestii poruszonej w tytule. Postawione w ten sposób pytanie nie da prostej i szybkiej odpowiedzi… będzie za to stanowiło impuls dla powołania do życia niniejszego artykułu.
Data publikacji: 23.09.2024
Data aktualizacji: 23.09.2024
Podziel się:
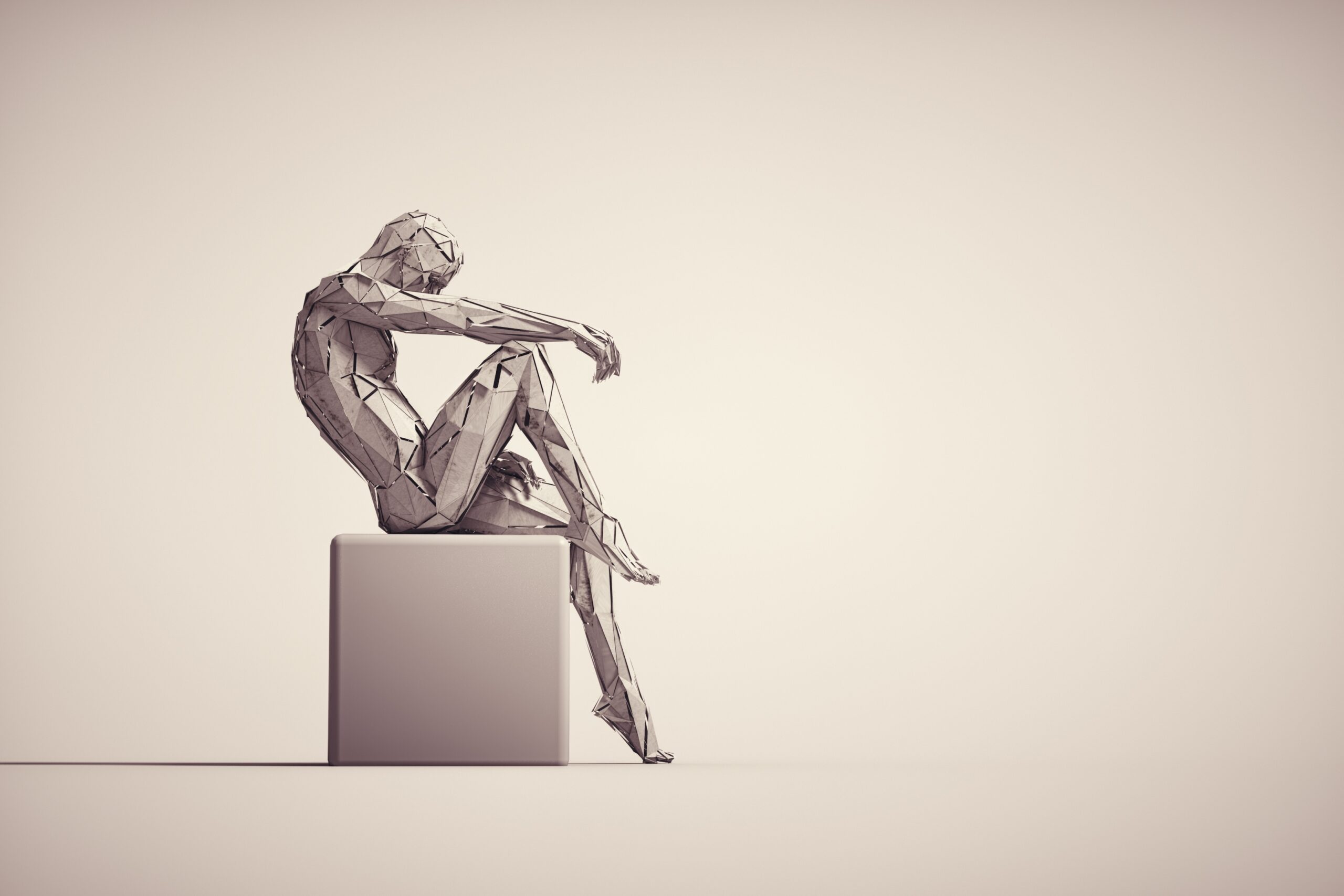
Zanim odpowiemy na pytanie „ile to kosztuje”, postarajmy się najpierw zrozumieć, za co chcemy zapłacić. Przedmiotem naszego zainteresowania jest magazyn – obiekt przeznaczony do składowania towarów i realizowania funkcji związanych z przepływem materiałów, zależnych od jego roli w łańcuchu dostaw. Posiada on określone fizyczne komponenty – przestrzeń zajętą przez infrastrukturę magazynową, przepływy materiałów, procesy oraz system zarządzania tymi procesami. Funkcje magazynu możemy realizować za pomocą prostych środków – niskonakładowego wyposażenia i infrastruktury oraz manualnych procesów. Niskie nakłady mają jednak swoje konsekwencje, np. dużą liczbę personelu, wymagają też z reguły większej przestrzeni. Przy zwiększonej skali przepływu materiałów stają się one poważną przeszkodą dla wymaganej wydajności magazynu.
I tu pojawia się szansa dla automatyzacji, czyli wprowadzenia technologii mających na celu zastąpienie ludzkiej pracy urządzeniami oraz oprogramowaniem, aby poprawić wydajność, precyzję i niezawodność wykonywanych zadań, a także zwiększyć gęstość składowania towaru w przestrzeni magazynowej. Zanim automatyzacja przyniesie nam korzyści, czeka nas jednak szereg etapów złożonego projektu, z którym związane są nakłady i koszty.
Etap 1: Koncepcja i studium opłacalności
Pierwszym krokiem jest podjęcie decyzji o inwestycji w automatykę. Należy podjąć ją na podstawie analizy kosztów i potencjalnych oszczędności, jakie wdrożenie może nam przynieść. W zestawieniu z niezbędnymi nakładami i kosztami określamy stopę zwrotu stanowiącą, oprócz kryteriów niepieniężnych, podstawę dla tej decyzji.
Należy zatem opracować projekt koncepcyjny, dobrać optymalne technologie i poziom automatyzacji, a także porównać to z rozwiązaniem manualnym. W tym celu dla opracowanej koncepcji niezbędne jest zarówno oszacowanie budżetu inwestycyjnego i innych kosztów związanych z wdrożeniem (poniekąd o nich jest ten artykuł), jak i obliczenie oszczędności. Sam projekt koncepcyjny też kosztuje – to pierwszy, relatywnie niski koszt związany z naszą inwestycją, który należy ponieść bez względu na to, czy dojdzie ona do skutku, czy nie. Jest on konieczny jako podstawa decyzji o poniesieniu pozostałych, dużo wyższych kosztów.
Etap 2: Projekt detaliczny i przetarg
Skoro decyzja jest na „tak”, przystępujemy do projektowania detalicznego. Inwestycja w automatykę to nie tylko sama technologia magazynowa. To również budynek (lub jego adaptacja) i technologie z nim związane oraz narzędzia informatyczne. Wszystkie te komponenty inwestycji należy zaprojektować i zadbać o synchronizację poszczególnych branż projektu: zarówno fizyczne interfejsy pomiędzy technologią magazynową, budynkiem i technikami z nim związanymi (oświetlenie, HVAC, ppoż, itp.), jak i informatyczne interfejsy pomiędzy systemami IT. W procesie przetargu wybieramy dostawców i wykonawców. Projekt detaliczny i przetarg to kolejne etapy procesu inwestycyjnego i zarazem kolejne koszty z tą inwestycją związane.
Etap 3: Realizacja i testy
Po wyborze dostawców i wykonawców oraz podpisaniu umów realizowane są projekty wykonawcze i rozpoczyna się produkcja wyposażenia magazynu, a następnie montaż na miejscu. Równolegle prowadzone są prace związane z realizację lub adaptacją budynku oraz przygotowanie systemów informatycznych zarządzających instalowaną automatyką – od opracowania specyfikacji funkcjonalnych, przez programowanie i parametryzację, po testy funkcjonalne. Po zakończeniu montażu i testów zainstalowanego wyposażenia następują testy integracyjne z systemami informatycznymi i jesteśmy gotowi do uruchomienia. Ten etap inwestycji kosztuje nas najwięcej – nakłady na instalowane wyposażenie, budynek, systemy IT, do tego koszty związane z zarządzaniem projektem, szkoleniami i migracją do nowego obiektu.
Jakie elementy procesów magazynowych zautomatyzować w pierwszej kolejności?
Automatyzacja procesów magazynowych jest kluczem dla zwiększenia wydajności i konkurencyjności. Każde przedsiębiorstwo ma specyficzne potrzeby, dlatego automatyzacja wymaga zawsze indywidualnego podejścia. Oto obszary, które warto zautomatyzować w pierwszej kolejności.
- Transport wewnętrzny towarów – automatyzacja z wykorzystaniem autonomicznych pojazdów mobilnych, takich jak MIR, we współpracy z regałem automatycznym Lean-Lift zyskuje coraz większe zainteresowanie. Systemy te zapewniają bezpieczne i szybkie przemieszczanie towarów, eliminując błędy ludzkie i skracając czas realizacji zamówień. AMR działają przez całą dobę, optymalizując procesy logistyczne i redukując koszty.
- Składowanie towarów wielkogabarytowych i o dużej masie – dla firm przechowujących ciężkie i duże materiały, takie jak blachy czy dłużyce, automatyczne systemy magazynowe LogiTower oferują dużą wydajność, maksymalizując wykorzystanie przestrzeni magazynowej, a także zapewniając bezpieczną obsługę ładunków.
- Załadunek i rozładunek blach – automatyzacja tych procesów przy użyciu systemu LogiTowerLoader eliminuje przestoje wycinarek laserowych, zwiększając efektywność operacyjną i przyspieszając produkcję.
- Kompletacja zamówień – automatyczne regały, takie jak Rotomat czy Lean-Lift, przyspieszają dostęp do produktów, redukując czas kompletacji i minimalizując ryzyko pomyłek.
- Magazynowanie narzędzi i części zamiennych – systemy Lean-Lift zapewniają gęste składowanie różnej wielkości towarów (fotokomórki mierzące wysokość produktów na półkach), co znacznie oszczędza powierzchnię, a także ułatwia dostęp do składowanych towarów.
ISL I LogiTower projektuje i wdraża systemy automatyczne, które optymalizują magazynowanie i logistykę produkcji. Więcej informacji: isl.pl oraz logitower.eu.
Aneta Kępka
Marketing Manager
ISL I LogiTower
Etap 4: Uruchomienie i stabilizacja
Uruchomienie wdrożenia nie oznacza jeszcze zakończenia procesu inwestycyjnego. Rozruch ze zmniejszoną wydajnością pozwala na usunięcie błędów, kontynuację procesu szkolenia personelu operacyjnego i technicznego, a następnie testy wydajności i dyspozycyjności. Po stabilizacji pracy magazynu z nowym wyposażeniem i oprogramowaniem, usunięciu wszelkiego rodzaju błędów i zamknięciu list otwartych punktów, następuje odbiór końcowy i stopniowy wzrost wydajności do osiągnięcia założonych celów.
Od tego momentu automatyka zaczyna spłacać swój dług przez generowanie oszczędności w nakładach pracy ludzkiej, większej produktywności i dokładności. Podsumujmy zatem składniki tego długu, czyli składniki budżetu na wdrożenie automatyki.
Budżet na automatykę
Konstruując budżet na zaprojektowanie i wdrożenie automatyki, musimy uwzględnić następujące jego komponenty:
- Nakłady na technologię przepływu materiałów i składowania towaru, w tym:
- systemy transportu wewnętrznego i sortowania – przenośniki, autonomiczne roboty mobilne, windy, sortery, itp.,
- automatyczne systemy składowania i kompletacji – ASRS, shuttle, miniload, Cube/Autostore, regały karuzelowe, stacje kompletacyjne i wiele innych,
- systemy automatycznego handlingu – roboty paletyzujące i depaletyzujące, stackery/destackery roboty współpracujące, (coboty), itp.,
- urządzenia do automatycznej identyfikacji i pomiaru towaru – skanery, kamery, etykieciarki, bramki RFID, stacje kontroli konturów, wagi, itp.,
- wszelkie urządzenia pomocnicze, takie jak stacje Order Start, automatyczne bufory pustych nośników, urządzenia do pakowania, zamykania foliowania i plombowania jednostek ładunkowych, drony magazynowe do inwentaryzacji i inspekcji oraz wszelkie inne rozwiązania niemieszczące się w wyżej wymienionych kategoriach/
- Nakłady i koszty IT, w tym:
- software – system zarządzania magazynem (WMS), placem manewrowym (YMS), system sterowania przepływem materiałów (MFC) i zarządzania instalacjami budynku (BMS), oprogramowanie do analizy danych i raportowania; nakłady i koszty związane z oprogramowaniem obejmują kupno licencji, niezbędnego programowania i parametryzacji oraz testów,
- hardware – serwery i serwerownie lub koszty usług w chmurze, urządzenia peryferyjne i infrastruktura sieciowa.
- Nakłady związane z budynkiem i jego otoczeniem:
- budowa nowego lub adaptacja istniejącego budynku i działki,
- wyposażenie i technologia budynku – ppoż, wentylacja, ogrzewanie i klimatyzacja (HVAC), inteligentne oświetlenie, kontrola dostępu, CCTV, itp.,
- zasilanie w energię – przyłącze do sieci energetycznej, zasilacze awaryjne i generatory, inwestycje w rozwiązania zwiększające efektywność energetyczną, w tym wykorzystanie energii odnawialnej.
- Koszt planowania i wdrożenia, w tym koszty związane z zaangażowaniem własnego personelu i dodatkowymi zadaniami związanymi z projektem:
- szkolenie personelu – szkolenia dla pracowników dotyczące obsługi nowych systemów i technologii,
- projektowanie i konsulting,
- zarządzanie projektem i koordynacja prac,
- testy i odbiory,
- migracja fizyczna – przeniesienie towaru do nowego magazynu lub jego części,
- migracja informatyczna – cutover, migracja danych do środowisk produkcyjnych, usunięcie danych testowych.
- Rezerwa na nieprzewidziane wydatki i ryzyka – rezerwy finansowe na niespodziewane problemy i opóźnienia.
Koszty automatyzacji obejmują szereg elementów, które różnią się w zależności od zastosowanego systemu. Kluczowe składniki kosztowe to:
- Koszty inwestycyjne – są to wydatki na zakup sprzętu i oprogramowania. W przypadku zaawansowanych systemów, takich jak CVP Impack i CVP Everest, które automatyzują proces pakowania, koszty te obejmują zakup samych urządzeń oraz ich instalację. Obie maszyny oferują różne poziomy możliwości i wydajności, co wpływa na ich cenę.
- Koszty oprogramowania – systemy CVP wymagają specjalistycznego oprogramowania do zarządzania procesami pakowania. Obejmuje to licencje, koszty aktualizacji, a w przypadku bardziej złożonych konfiguracji również rozwój dedykowanych aplikacji do integracji z istniejącymi systemami.
- Koszty szkolenia – wdrożenie systemów takich jak CVP Impack i CVP Everest wymaga przeszkolenia personelu w zakresie obsługi nowych technologii. Szkolenia te mogą dotyczyć operatorów maszyn oraz personelu technicznego, co wiąże się z dodatkowymi kosztami.
- Koszty utrzymania i serwisu – systemy automatyzacji, w tym CVP, wymagają regularnej konserwacji i serwisowania, aby zapewnić ich niezawodność. Dodatkowo mogą wystąpić koszty związane z aktualizacjami oprogramowania oraz dostosowaniem maszyn do zmieniających się potrzeb produkcyjnych.
- Koszty adaptacji infrastruktury – w niektórych przypadkach, aby zainstalować zaawansowane systemy pakowania, konieczne jest dostosowanie infrastruktury, np. modernizacja sieci elektrycznych lub zmiana układu linii produkcyjnej, co generuje dodatkowe wydatki.
Każdy z tych elementów składa się na całkowity koszt automatyzacji, który może się różnić w zależności od wybranego systemu i skali wdrożenia.
Robert Kostera
Country Business Development Manager
Sparck Technologies Polska
Koszty automatyzacji – podsumowanie
Wszystkie powyższe nakłady i koszty należy umiejętnie oszacować oraz zestawić z równie umiejętnie oszacowanymi korzyściami z wdrożenia automatyki, takimi jak zwiększenie efektywności operacyjnej, redukcja kosztów pracy, zwiększenie dokładności i skrócenie czasu realizacji zamówień. W tym bilansie nakładów i korzyści nie można zapominać o kosztach generowanych przez automatykę już po jej uruchomieniu, np.:
- koszt zużywanej energii,
- utrzymanie serwerów lub usługi w chmurze,
- aktualizacje i utrzymanie oprogramowania – koszty licencji, subskrypcji i aktualizacji oprogramowania,
- konserwacja i serwis – utrzymanie ruchu, naprawy i serwisowanie urządzeń.
Jak widać, mamy do czynienia z mnogością różnorodnych kosztów i nakładów inwestycyjnych. Dodatkowo w ramach każdego z wymienionych komponentów kosztowych mówimy o znacznej rozpiętości możliwego budżetu. Zależy ona od poziomu automatyzacji, zastosowanych technologii, zakresu procesów objętych automatyzacją, czy wreszcie od wyboru konkretnego dostawcy. Dlatego podejmując decyzję o wydaniu niebagatelnych pieniędzy, nie należy iść na skróty, lecz starannie przeprowadzić proces analizy opłacalności i planowania koncepcyjnego. A następnie, po pozytywnej decyzji, przejść przez kolejne etapy realizacji inwestycji, nie zaniedbując żadnego z nich – najlepiej ze wsparciem niezależnych ekspertów.
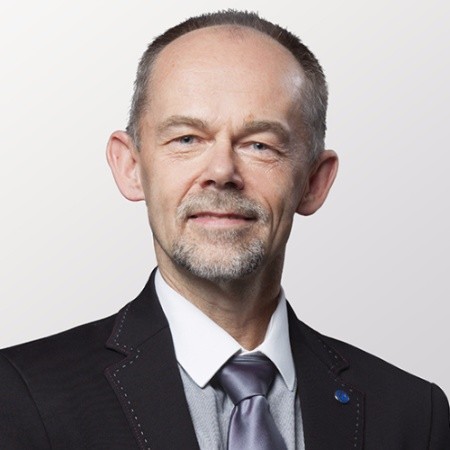
Jacek Olszewski
Senior Principal & Partner
Miebach Consulting
Jestem Partnerem i Starszym Konsultantem w Miebach Consulting, międzynarodowej firmie konsultingowej specjalizującej się w inżynierii łańcucha dostaw. Moja praca koncentruje się na planowaniu centrów dystrybucyjnych, poprawie procesów przepływu materiałów i logistyce produkcji. Zajmuję się również strategicznymi projektami logistycznymi, takimi jak optymalizacja sieci dystrybucji, zarządzanie zapasami i procesy łańcucha dostaw. Mam doświadczenie w różnych branżach, m.in. w przemyśle lotniczym, napojowym, FMCG, kosmetycznym i high-tech. Wykonałem ponad 100 projektów dla tych branż na rynkach międzynarodowych. Poza pracą lubię biegać maratony, tańczyć sambę, jeździć na nartach oraz zajmować się sztuką i fotografią.
Zobacz również