SUPPLY CHAIN, INTELIGENTNE TECHNOLOGIE
IoT bez kabli i komplikacji
O praktycznych zastosowaniach rozwiązań IoT w cyfryzacji łańcuchów dostaw z Michałem Kowalskim, Partner – Sales & Business Development Sigfox Poland, rozmawia redakcja „Logistics Managera”.
Data publikacji: 17.07.2025
Data aktualizacji: 17.07.2025
Podziel się:
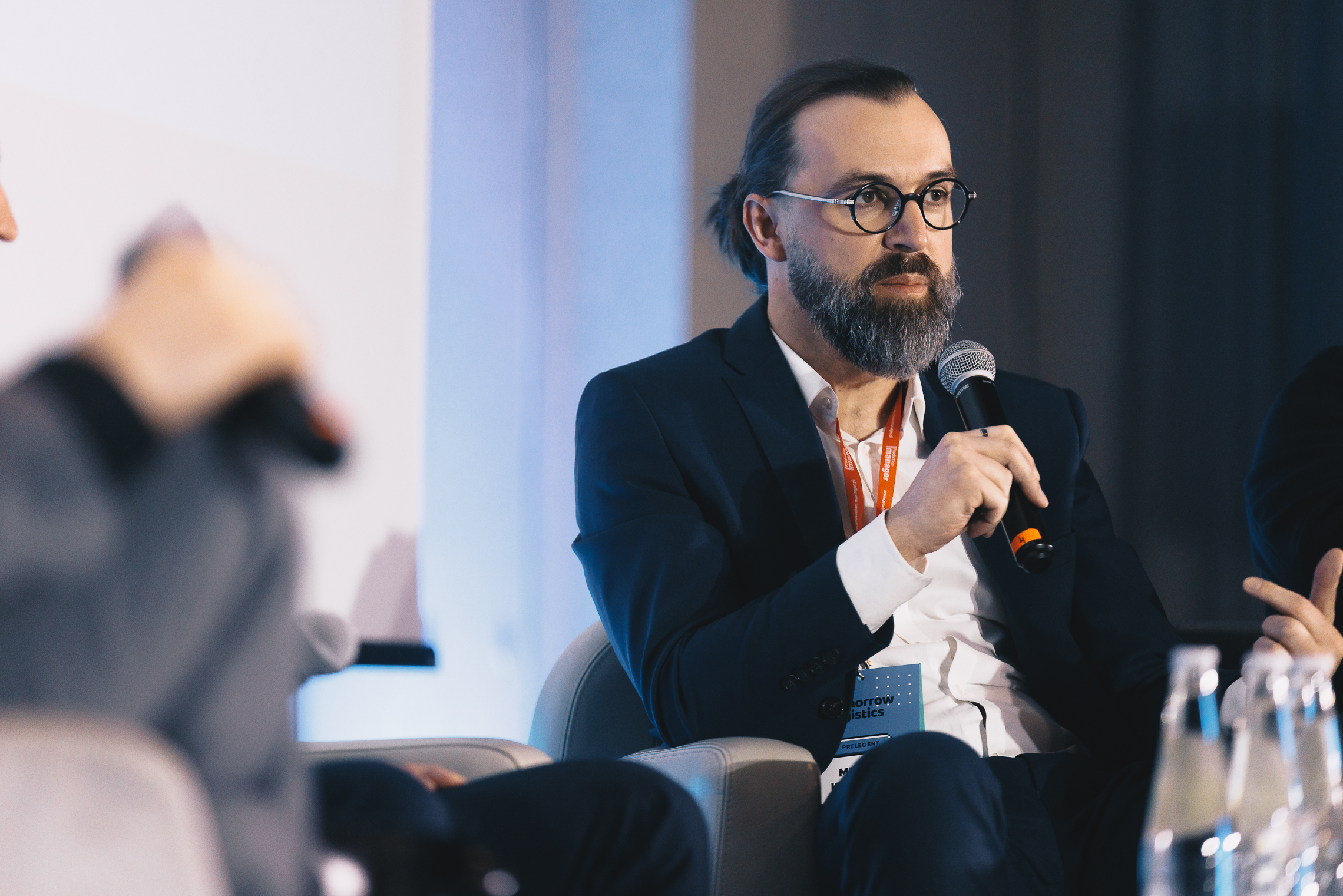
Logistics Manager: Czym dokładnie są oferowane przez Sigfox systemy IoT?
Michał Kowalski: To rozwijane od wielu lat platformy przeznaczone do optymalizacji procesów biznesowych – w obszarze logistyki do monitorowania i śledzenia obiektów, których do tej pory nie udawało się monitorować z powodu ograniczeń technologii (np. RFID). Platformy są zasilane przez w pełni bezprzewodowe czujniki (np. trackery) funkcjonujące 5–7 lat bez konieczności wymiany baterii – poza lokalizacją dostarczają informacje o temperaturze, otwarciu ładunków, uderzeniach itp. Dynamiczny rozwój technologii sprawia, że część tych urządzeń funkcjonuje dzisiaj w formie jednorazowej, np. do monitorowania przesyłek. Na bieżąco przesyłają dane, a po zakończeniu transportu są zwyczajnie utylizowane.
LM: Kto najczęściej korzysta z Waszych rozwiązań? Dla jakich firm są one stworzone?
MK: Nasi klienci to firmy posiadające łańcuchy dostaw, np. sieci retail, firmy FMCG, automotive, kurierskie. W ich łańcuchach dostaw funkcjonują zarówno własne punkty – fabryki, centra dystrybucyjne – jak i punkty partnerów zewnętrznych – podwykonawców, firm logistycznych, kurierskich itp. Złożoność ich procesów sprawia, że zastosowanie RFID staje się niemożliwe. W tej grupie naszych klientów są m.in. Castorama Polska, Kirchhoff Automotive, ZING, DPD Fresh oraz LOT AMS (część Polskiej Grupy Lotniczej). Inna grupa klientów to firmy logistyczne, które wykorzystują np. jednorazowe aktywne czujniki IoT do zabezpieczania swoich transportów oraz wykrywania wszelkich nieprawidłowości, dając możliwość zareagowania we właściwym momencie.
LM: W jakich obszarach łańcucha dostaw technologia Sigfox sprawdza się najlepiej?
MK: Monitorowanie i zarządzanie opakowaniami zwrotnymi, śledzenie przepływów nośników w procesach intralogistycznych, np. przy zasilaniu gniazd produkcyjnych, zarządzanie środkami trwałymi. Nasi klienci monitorują kontenery na śmieci, naczepy, swap-bodies czy sprzęt wykorzystywany do handlingu samolotów. Ostatnio klienci zaczęli wykorzystywać jednorazowe czujniki do audytu swoich procesów logistycznych – monitorowania podwykonawców czy dostawców komponentów. Kolejny obszar to efektywność energetyczna oraz zbieranie danych na potrzeby raportowania ESG.
LM: Jakie przewagi w porównaniu z innymi rozwiązaniami kryją się w Waszej technologii?
MK: Pełna bezprzewodowość rozwiązań – brak infrastruktury umożliwia pełne wdrożenie bez wpływu na realizację bieżących operacji. Autonomiczność rozwiązań – czujniki IoT funkcjonują wiele lat bez konieczności wymiany baterii (5–7 lat to standardowy okres). Modułowość pozwala rozbudowywać systemy wraz ze zmieniającymi się potrzebami klientów oraz otoczeniem rynkowym. Zasięg działania – mamy projekty, w których klienci na bieżąco monitorują swoje obiekty na różnych kontynentach. Na koniec – doświadczenie. W samej logistyce w naszych platformach lub przy wykorzystaniu naszych technologii monitorowanych jest kilkanaście milionów obiektów.
LM: Pisanie własnego oprogramowania czy aplikacja w modelu SaaS?
MK: Dobre pytanie. Zdecydowanie aplikacja w modelu SaaS – dostępna dla klientów od pierwszego dnia. Nasze systemy IoT od 7–10 lat są rozwijane stricte pod kątem zastosowań w cyfryzacji łańcuchów dostaw, z uwzględnieniem specyfiki uzyskiwanych danych, raportowania, wykrywania nieprawidłowości czy optymalizacji procesów. Otwarte API ułatwia wymianę i synchronizację z systemami WMS / TMS / ERP czy YMS. Próba rozbudowy systemów WMS czy ERP o funkcjonalności IoT kończy się zawsze tak samo – projektami trwającymi miesiące lub kwartały, wysokimi nakładami inwestycyjnymi i ryzykami towarzyszącymi klasycznym projektom IT. Wszystko przez to, że zwrot z inwestycji przekracza 4–5 lat, a późniejsze koszty utrzymania są wyższe od wykorzystania naszych platform.
LM: Trudno rozpocząć taki projekt?
MK: Klienci często chcą przetestować przed pełnym wdrożeniem. Ponieważ nasze rozwiązania są w 100% bezprzewodowe i nie wymagają budowy skomplikowanej infrastruktury oraz złożonych integracji (jak to ma miejsce w przypadku RFID), uruchomienie testów to zazwyczaj pojedyncze godziny pracy, łącznie ze szkoleniem dla użytkowników. Testy przyjmują np. formę miniwdrożenia (np. na 50–100 opakowaniach zwrotnych). Po 4–8 tygodniach testów mamy wystarczająco dużo danych do zbudowania ROI dla pełnego wdrożenia.
LM: Jakie konkretne korzyści mają klienci z wdrażania Waszych rozwiązań?
MK: Pełna widoczność w łańcuchach dostaw to otwarcie drogi do szeregu optymalizacji. Zwiększenie stopnia wykorzystania oraz krótsze cykle opakowań (od plastikowych palet do olbrzymich kontenerów) pozwala uwolnić zamrożony CAPEX oraz uniknąć konieczności rozbudowy floty wraz ze zwiększaniem skali działania. Wykrywanie przestojów lub ryzyka zerwania łańcucha dostaw – informacja o braku nośników przy produkcji uniemożliwiających załadunek gotowych wyrobów lub brak kontenerów do przesłania paczek do innego centrum logistycznego – już same te obszary gwarantują, że zwrot z inwestycji w tego typu rozwiązania liczony jest w miesiącach. Automatyzacja pracy – inwentaryzacja (zarówno nośników, jak i przechowywanych w nich towarów) odbywa się automatycznie kilka razy dziennie, bez względu na lokalizację obiektu w łańcuchu dostaw, dając dane, które do tej pory były albo niedostępne, albo wymagały uzyskiwania informacji od innych uczestników łańcuchów dostaw. Optymalizacja kosztów transportu – dokładna wiedza o statusie poszczególnych elementów łańcucha dostaw sprawia, że dokładniej możemy planować odbiór pustych nośników (np. stojaki na okna) lub wysyłkę gotowych produktów. Eliminacja ręcznej pracy – wszystkie informacje dostępne są automatycznie, bez konieczności ręcznego skanowania, wysyłania maili czy wykonywania telefonów do partnerów. Poza automatyzacją eliminujemy ryzyka związane z ręcznym wpisywaniem danych.
LM: Jak szybko zwracają się Wasze rozwiązania?
MK: Ostatnio z Castorama Polska mieliśmy przyjemność prezentować efekty wdrożenia naszego rozwiązania do zarządzania opakowaniami zwrotnymi – okres zwrotu poniżej 15 miesięcy i oszczędności sięgające setek tysięcy euro przy czasie wdrożenia zamykającym się łącznie w kilkunastu dniach.
LM: Dziękujemy za rozmowę.
Zobacz również